- Project
- SHERLOCK
- News
Seamless and safe human - centred robotic applications for novel collaborative workplaces
Back to project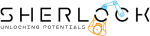
“ROS drivers suite” for COMAU robots
ROS, which stands for Robotic Operating System, is an open-source robotics middleware. Nowadays, it is increasingly being used in research as well as industrial applications due to the flexibility it offers. ROS provides peer-to-peer communication among various devices, is lightweight and supports multiple programming languages.
SHERLOCK consists of 19 hardware and software modules. Following a versatile approach, communication among the modules is being achieved via ROS, either using existing ROS interfaces or building them from scratch.
In this context, LMS developed the necessary drivers that provide ROS support for the COMAU AURA and Racer5L cobots, enabling their communication with the rest of the SHERLOCK ecosystem.
The developed “ROS drivers suite” offers the following main features:
- Asynchronous robot control
- I/O control
- Fieldbus control
- Synchronous robot control (sensor tracking)
Asynchronous robot control: The robot publishes its state to the ROS driver with a frequency of 100Hz. During this operation, two ROS action servers are responsible for moving the robot, one for joint space trajectories and one for cartesian space trajectories. The desired trajectory is sent from the ROS application (e.g., MoveIt) as a goal for the robot. Functionalities such as validation that the goal is inside the robot limits and that it is ready to receive a new goal are also implemented.
I/O control: This part of the “ROS drivers suite” is responsible to enable/disable the hard-wired I/Os of the robot. A dedicated ROS service offers control over the physical of virtual GPIO pins of the controller while providing feedback regarding their state.
Fieldbus control: This part of the “ROS drivers suite” is responsible to control devices connected to the robot controller via Fieldbus (PROFINET, PROFIBUS, Ethernet IP), as well as monitor their state.
Synchronous robot control (sensor tracking): The difference of the synchronous robot control compared to the asynchronous one is that in the synchronous control, the robot is correcting its trajectory in real-time based on feedback received from dedicated sensors (force/torque sensors, vision systems etc.) The control loop frequency can be as high as 500 Hz, ensuring quick and smooth corrections. The user (ROS application) can move from asynchronous to synchronous robot control mode at any time.
“ROS drivers suite” includes two more applications. The “COMAU robot simulator” which allows the user to perform a simulation for a given application without the need of a physical robot, and the “MoveIt interface” which enables the on-the-fly trajectory planning (either in physical or virtual application).
It is worth noting that, apart from the AURA and the Racer5L robots, this “ROS drivers suite” supports a variety of COMAU robots that use the C5G controller, such as NJ4 110-2.2, NJ4 170-2.9, NJ 220-2.7, Racer 5-0.80, Racer 7-1.4.
For more information, you may visit the website of the project.
Photos --> link 1
COMAU Racer5 Cobot released to the market!
SHERLOCK is pleased to announce the first, early, commercially exploitable result of the project, COMAU Racer5 Cobot, a new paradigm in collaborative robotics, designed and commercialized by COMAU.
COMAU, a well-known Italian robotics manufacturer and industrial partner of SHERLOCK, just released to the market their newly developed low-payload collaborative robot.
Driven by the requirements of the industrial use cases of SHERLOCK, aligned with the market needs, COMAU developed within the project a low payload collaborative robot with payload of 5Kg.
It is currently the only collaborative robot able to automatically switch from industrial robot speed to collaborative speed. This feature allows it to work in full -industrial- speed when the operator is far away from the robot while reducing its speed to lower -collaborative- speed when the operator enters its working area. Thus, increased flexibility and productivity, as well as reduction of cycle time, can be achieved.
Moreover, Racer5 cobot offers an intuitive, non-intrusive programming framework. The operator is able to effortlessly move the end effector and teach robot motion using hand guidance.
Racer5 cobot is a certified product, complying with all the safety derivatives relevant with human-robot collaboration.
For more information, you may visit our website.