News Dashboard
News
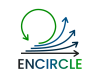
1st Press Release
The ENCIRCLE project officially kicks off to revolutionize sustainable manufacturing
Date: 6 November 2024
Location: Thessaloniki, GREECE
The European Union-funded project “Enabling Circular Value Chains via Production Digitization and Human Empowerment” (ENCIRCLE) officially launched on the 1st of October 2024. The ENCIRCLE project is setting a new benchmark in sustainable manufacturing by offering an advanced framework for environmental impact assessment. This European initiative leverages state-of-the-art technologies, including Digital Twins, Soft Sensors, and Digital Product Passports, to transition traditional manufacturing methods toward sustainable, circular models. The ENCIRCLE project is supported by the Horizon Europe Research and Innovation Action (RIA) under Grant Agreement No 101178230, and will run for three years, bringing together a dynamic consortium of 15 partners across Europe, including top research institutions, industry leaders, and specialized SMEs.
The kick-off meeting, held on 29 and 30 of October 2024 in Thessaloniki, Greece, gathered all partners to outline objectives, defined roles, and set the project’s anticipated impact towards transitioning from linear to circular manufacturing by building on and advancing digital technologies. The ENCIRCLE project aims to:
- Decarbonize manufacturing, searching for sustainable production configurations and designs that reduce environmental footprint without compromising quality.
- Train workforce through gamification, cultivating new skills and fostering a new circular mindset.
- Follow a human-centered design and propose a symbiotic ecosystem of humans and AI through explainable Human-in-the-Loop methodologies.
Aligned with the EU’s guidelines on sustainable production, ENCIRCLE emphasizes a strategic approach to circularity at each stage of the product lifecycle, with key objectives focusing on:
1. AI-enabled control loops for sustainable manufacturing
2. Circularity and Life Cycle Assessment (LCA) Framework
3. Production virtualization for first-time right manufacturing
4. Human-in-the-Loop (HITL) Decision Support System
5. Gamification for circular value chains
6. Digital Product Passport (DPP)
With the achievement of the above objectives, ENCIRCLE’s end goal is to create a culture of sustainable consumption and responsible production, encouraging businesses to adopt circular CRM systems and empowering consumers with digital tools for sustainable choices. By exploring legal and ethical dimensions, the project is committed to creating a model for the industry that aligns with the environmental needs of the planet, ultimately contributing to the global effort of mitigating climate change and fostering a sustainable economy.
For more information, please visit the project website (www.encircle-project.eu) and/or contact the project coordinator:
Dr. Nikolaos Dimitriou
e-mail: nikdim@iti.gr
3rd Internal Workshop: Life Cycle Assessment of the three GREEN-LOOP value chains | 27 January 2025
The 3rd internal workshop on Life Cycle Assessment (LCA) within the GREEN-LOOP project took place on January 27, focusing on the LCA of the three value chains involved in the project. This session aimed to provide a deeper understanding of LCA methodologies and their application to sustainable manufacturing systems based on novel bio-based materials. This workshop was designed to equip participants with both theoretical and practical insights into LCA, emphasizing its importance in assessing the environmental impact of materials throughout their entire life cycle. Trainers from AIMEN, Carlos Bernárdez Casás and Rocío Pena Rois, led the session, delivering key knowledge on the methodology, tools, and applications of LCA within the GREEN-LOOP project.
The workshop was conducted online via Microsoft Teams and incorporated interactive elements through tools such as PowerPoint and Mentimeter. Over the course of 1 hour and 10 minutes, participants explored several core aspects of LCA, including:
- Fundamental concepts of Life Cycle Assessment – An overview of what LCA entails and its significance in sustainability assessments.
- Application of LCA to the three GREEN-LOOP value chains – A detailed examination of how LCA is integrated into the project to evaluate material impact.
- Tools and methodologies for conducting LCA – Insights into key instruments used to assess the environmental performance of materials.
The session began with an introduction and ice-breaking activity, allowing participants to engage before diving into the core topics. This was followed by an explanation of the LCA framework, its relevance to the GREEN-LOOP value chains, and a discussion on the practical application of LCA tools. This internal workshop aligns with GREEN-LOOP’s broader objectives of promoting sustainable manufacturing practices and evaluating the lifecycle impact of bio-based materials. By integrating LCA into decision-making processes, the project seeks to enhance the sustainability of materials across different stages of production and use. The insights shared in this workshop will contribute to ongoing efforts in optimizing the environmental footprint of materials within the GREEN-LOOP framework. Future sessions will continue to build on these discussions.
Introduction to Sustainable Materials in Product Design | 3-4 December 2024
On December 3rd and 4th, 2024, the 2nd Internal Workshop on “Introduction to Sustainable Materials in Product Design” took place virtually, hosted by Marcus Crew from the National Composites Centre, in Bristol (UK).
Over the course of two mornings, participants explored the importance of sustainability in product design and examined strategies for integrating sustainable practices into their everyday processes.
The workshop highlighted key sustainable design principles, emphasiszing the increasing need for environmentally responsible choices. The sessions were designed to enhance knowledge, develop practical skills, and cultivate the right attitudes necessary to drive meaningful change in product development.
Key topics covered included the fundamentals of sustainability, focusing on the three pillars of sustainability and their application in design. Participants also assessed the impact of global warming and greenhouse gases on the environment, learning methods to mitigate these effects. Additionally, they explored tools to measure and implement circular design practices, as well as practical approaches to embedding sustainability throughout the product lifecycle via Design for Sustainability (DfS). Demonstrations of eco-design tools and software provided hands-on experience to support sustainable design efforts.
Throughout the workshop, attendees engaged in discussions, Q&A sessions, and practical activities, including exploring concepts like Sustainable Development Goals (SDGs), Planetary Boundaries (PBs), and Doughnut Economics, to frame sustainability within a global context. Hands-on tasks allowed participants to apply circularity principles and evaluate real-world sustainability applications in design.
By the end of the workshop, participants had gained a deeper understanding of sustainability’s role in product design and its environmental impact. They were equipped with practical tools and techniques, such as DfS and eco-design strategies, to implement sustainable practices in their own work. The workshop also provided valuable insights into current and future policies influencing sustainable product design.
Participants left the event inspired and ready to influence peers and organiszations, championing sustainable design tools and methodologies to amplify the initiative’s impact.
The success of the workshop highlights the importance of continuous learning and collaboration in addressing global challenges like climate change. It has laid a strong foundation for future exploration of sustainable practices, empowering participants to lead the transformation of product design into a force for environmental goods.
Stay tuned for more workshops and initiatives aimed at fostering sustainability in design and innovation!
Shaping a greener future: GREEN-LOOP’s Year 2024 in review
As 2024 comes to an end, we reflect on a year of remarkable progress, fruitful collaborations, and impactful achievements in our mission to foster circular and sustainable bio-based value chains. This year has been pivotal in advancing our shared vision of a greener and more sustainable future, with GREEN-LOOP playing a central role in key international events and conferences.
Here are some of the most significant milestones and achievements that have shaped our journey this year:
- Ecomondo 2024 (November 5th–8th, 2024): The GREEN-LOOP project was presented at Ecomondo 2024, one of Europe’s leading events on green technology and the circular economy. During the event, the project’s digital paper highlighted key results, fostering dialogue with industry leaders, policymakers, and researchers.
- Mirabilia Network Food & Drink Event (October 14th–15th, 2024): GREEN-LOOP proudly participated in the prestigious Mirabilia Network Food & Drink Event in Perugia, Italy. This global B2B gathering for the food and drink industry brought together leading companies and international buyers from markets worldwide, including the United States, Canada, Asia, and Europe. The event provided an excellent platform to promote sustainable practices and foster international cooperation in the food sector.
- 6th European Congress on Eco-Plasturgy and Sustainable, Intelligent, and Safe Plastic Materials (October 2nd–3rd, 2024): GREEN-LOOP contributed to the 6th European Congress on Eco-Plasturgy in Alessandria, Italy, offering valuable insights into plastics processing developments and applications, reinforcing its role in advancing sustainable solutions in the plastics sector.
- Macrolibrarsi Fest (September 21st–22nd, 2024): At Macrolibrarsi Fest in Cesena, Italy, GREEN-LOOP showcased its progress in developing bio-based materials to replace traditional plastic and aluminum caps in packaging. This event was an opportunity to engage directly with communities and showcase practical solutions.
- European Biomass Conference and Exhibition (EUBCE) 2024 (June 24th–27th, 2024): At EUBCE 2024 in Marseille, France, GREEN-LOOP shared insights on bio-based innovations and resource efficiency alongside five other projects from the BIO-MATTERS Cluster. Together, they presented manufacturing technologies for bio-based materials aimed at creating circular value chains for a wide range of final and intermediate bio-based products.
- National Stakeholder’s Workshop at Mixcycling (March 21th, 2024): In March 21th, the National Stakeholders’s workshop hosted by Mixcycling, in Breganze, highlighted the project’s efforts to improve sustainable production processes, with a focus on biomass valorisation for final bio-based products for different industries.
As we step into 2025, we extend our heartfelt gratitude to all our partners and stakeholders for their unwavering dedication and contributions to GREEN-LOOP’s success. The momentum we’ve built this year inspires us to continue pushing the boundaries of circular and bio-based innovation, creating lasting value for people and the planet.
GREEN-LOOP Project: Bio-based Solutions Compliant with the New European Packaging Regulation (PPWR)
Rimini (IT), November 7, 2024 – GREEN-LOOP is a European project that enhances the manufacturing industry by refining bio-based materials and optimising production processes to offer solutions compliant with the European Packaging and Packaging Waste Regulation (PPWR). Among the key players in the project is the Italian company Mixcycling, which transforms agricultural by-products into bio-based materials ideal for various applications, focusing on sustainable packaging. Another project partner, Guala Closures in Breganze (Vicenza, Italy), is actively involved in designing new products and testing Mixcycling’s bioplastics for bottle closures for spirits that comply with European regulations (EC 1935/2004 and 10/2011), ensuring safety for contact with food, beverages, and pharmaceuticals.
As part of the GREEN-LOOP project, a new bio-based composite for injection moulding was developed and used to create initial prototypes of screw caps and oil dispensers. Additionally, an innovative microwave-assisted production process helps reduce energy consumption and improve material properties. New bio-based thermoplastics incorporating agricultural residues as fillers also show great potential for packaging. These advancements were presented by the project’s dissemination leader, NSBproject, in the paper “GREEN-LOOP: Sustainable Bio-based Materials and Circular Economy Solutions” during the Ecomondo 2024 conference in Rimini on November 5, 2024.
Solutions for Packaging Companies Compliant with the Packaging and Packaging Waste Regulation (PPWR)
The European Packaging and Packaging Waste Regulation, approved on April 24, 2024, aims to promote the circular economy by reducing the environmental impact of packaging and waste. The main goals include reducing waste volumes by optimising use of materials and designs that avoid excessive packaging; promoting reuse with long-term solutions; and increasing the share of recycled materials by improving collection systems and recycling processes. These principles are crucial for environmental sustainability and natural resource conservation, contributing to reduced pollution and carbon footprint. The PPWR introduces stricter requirements to reduce waste and enhance recyclability, creating new challenges and opportunities for companies. GREEN-LOOP demonstrates how bio-based materials can play a significant role in this transition, offering alternatives to traditional plastics within the PPWR framework.
With support from NSBproject, Mixcycling has developed materials for packaging and food closures. In collaboration with Guala Closures, bioplastic composites have been integrated into tamper-evident closures that match conventional plastics in terms of strength, hygiene, and flexibility. These closures, compliant with EC regulations, are safe for use with food, beverages, and medicines, reflecting GREEN-LOOP’s commitment to regulatory compliance and the development of sustainable materials. Technologies such as microwave-assisted injection moulding, which reduces energy consumption by up to 30%, pave the way for sustainable solutions that meet the standards of fossil-based plastics. Collaboration with industrial partners showcases the feasibility of integrating bio-based materials across various sectors, from food to cosmetic packaging. The bio-based materials proposed in the GREEN-LOOP project could potentially replace recycled plastic content, either due to a lack of recycled material or for quality reasons. As stated in Art. 8 of the PPWR, within three years from the regulation’s entry into force, the European Commission will review the technological development status and environmental performance of bio-based plastic packaging, taking into account the sustainability criteria outlined in Article 29 of Directive (EU) 2018/2001 of the European Parliament and the Council. Based on this review, the Commission may propose legislation to:
a) establish sustainability requirements for bio-based raw materials in plastic packaging;
b) set targets to increase the use of bio-based raw materials in plastic packaging;
c) introduce the possibility of meeting the regulation’s objectives using bio-based plastic instead of post-consumer recycled content.
Conclusion
GREEN-LOOP will continue to develop solutions for bio-based industries by improving material formulations, optimising production processes, and conducting rigorous tests to ensure scalability and market readiness. For the packaging sector, the project’s outcomes will offer tangible solutions compliant with the new European Packaging and Packaging Waste Regulation (PPWR).
***
The GREEN-LOOP partners involved:
Guala Closures www.gualaclosures.com
Guala Closures offers high-quality, sustainable, and innovative closure solutions that ensure protection and convenience for end consumers while enhancing the value of brands. Guala Closures is a global leader in closures for the spirits, wine, beverages, oil, and condiments markets. With 35 production plants worldwide, the Group ensures proximity to its clients, offering tailored services and solutions. Guala Closures has over 5,000 employees.
Visit www.gualaclosures.com and follow the company page on LinkedIn.
MIXCYCLING www.mixcycling.com
Founded as a start-up in 2020 by brothers Gianni and Amerigo Tagliapietra, Mixcycling scaled up to become an industry player in 2023, earning international awards and recognition. It collaborates with major research centres and universities and participates in the GREEN-LOOP project funded by the European Commission, focusing on the research and development of high-performance, low-impact biopolymers (LCA – Life Cycle Assessment). Mixcycling’s technology is based on a patented process and proprietary technology that valorises organic waste and blends it with both bio-based and fossil-based materials, creating new raw materials for major industrial groups such as EssilorLuxottica, Stoelzle Glass Group, SCHID Spa, UniCredit StartLab, Adamo srl, Lavazza Group, Stilfibra srl, DeRoma Group, Selle Royal Group Spa, among others.
NSBproject www.nsbproject.com
NSBproject (NSB) supports large and medium-sized Italian enterprises in identifying, testing, and adopting innovative and enabling technologies, assisting with research, development, and technological innovation projects for products and processes. Leveraging a vast network of research entities and consortia across Europe and solid relationships with corporate partners and clients, NSB professionals contribute to the Italian and European innovation ecosystem with technological and financial scouting services. NSBproject is a partner in numerous Horizon Europe programme projects, serving as an Innovation Broker. Founded twenty years ago by professionals with expertise in technological innovation and extensive knowledge of national and European research and innovation funding mechanisms, CEO Fabrizio Riccomi, along with partners Andrea Jester and Rita Zanni, promotes and facilitates technology transfer, playing a key role in Italy’s economic system innovation, traditionally driven by foundations and universities. NSB is headquartered in Mantua, with offices in Veneto and Tuscany.
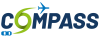
Aerospace and automotive waste can be turned into high-quality components for new products thanks to digital technology developed by the COMPASS project
Steyr, January 29, 2024
The COMPASS project, a collaborative effort among 13 leading European partners, was officially launched with a kick-off meeting held in Steyr, Austria, on January 23-24, 2024. Funded under the European Union’s HORIZON EUROPE programme, COMPASS aims to revolutionize the remanufacturing of sheet metal and thermoplastic composites, significantly reusing material waste for high-quality components production, and promoting a circular economy approach in the aerospace and automotive industries. The PROFACTOR research team, coordinator of the project, stated that: “The digital tools developed in COMPASS will make disassembly processes efficient for extracting sheet metal or panels from a decommissioned aircrafts or cars, where relevant component information will be collected and stored in the digital passport during the part’s life-cycle. In addition, remanufacturing process planning software will also optimize the matching of incoming and outgoing parts for the creation of new products”.
Below we present the key concepts of the project:
Driving Circularity through Advanced Remanufacturing
The COMPASS project addresses the growing challenge of efficiently recycling and remanufacturing components at the end of their lifespan. By employing advanced remanufacturing techniques, COMPASS will extend the life of these components, minimizing the need for raw material extraction and reducing environmental impact of new component production.
A Data-Driven Approach for Enhanced Remanufacturing
COMPASS introduces a novel data-driven approach to remanufacturing, leveraging digital tools and a comprehensive digital component passport. This passport will capture real-time information about component performance and history, enabling intelligent remanufacturing strategies. Optimizing Remanufacturing Processes and Quality Digital tools will streamline dismantling processes, ensuring efficient extraction of sheet metal and composite panels. The passport will also facilitate the collection of relevant component data, facilitating improved quality control and optimization of remanufacturing operations.
Partnership for Innovation and Impact
COMPASS brings together a diverse consortium of experts from academia, research institutions, and industry, representing Austria, Netherlands, Spain, Italy, and Germany. This collaboration will bring together cutting-edge technologies and expertise to develop and drive innovation in remanufacturing processes.
Achieving Sustainable Manufacturing for the aerospace and automotive sectors
The COMPASS project aims to achieve a significant impact by enabling the remanufacturing of approximately 30% of sheet metal parts and thermoplastic composite panels. The remanufacturing process will utilize end-of-life components, or production scrap, from aircraft or cars, retaining a high value in sheet metal and composite panels, rather than reprocessing them as secondary raw materials and/or sending them to landfill. The total commercial value will be in the order of EUR 60 million per year (30,000t/year of end-of-life scrap and 14,000t/year of production scrap) for metal alloys and EUR 500 million per year for composites (10,000t/year) by 2035. This will lead to substantial resource savings and contribute to a more sustainable future for the aerospace and automotive sectors. This will lead to substantial resource savings and contribute to a more sustainable future for the aerospace and automotive sectors.
Project Summary
Project Title: A Data-driven remanufacturing process for sheet metal and thermoplastic composites
Project Acronym: COMPASS Project Number: 101136940
Funding Programme Call – type of action: HORIZON-CL4-2023-TWIN-TRANSITION-01 - Innovation Actions Project
Starting Date: January 1, 2024
Project End Date: December 31, 2026
Project Duration: 36 months
Partners:
PROFACTOR GMBH (Austria) – Project Coordinator
CIRCULARISE BV (Netherlands) FACC OPERATIONS GMBH (Austria)
AIRCRAFT END-OF-LIFE SOLUTIONS BV (Netherlands)
KONINKLIJK NEDERLANDS LUCHT- EN RUIMTEVAARTCENTRUM - NLR (Netherlands)
AIT AUSTRIAN INSTITUTE OF TECHNOLOGY GMBH (Austria)
NSBPROJECT SRL – NSB (Italy)
MARK METALLWARENFABRIK GMBH (Austria)
FUNDACION AITIIP (Spain)
EDAG ENGINEERING GMBH (Germany)
SCHILD & PARTNER GMBH (Austria)
VOESTALPINE METAL FORMING GMBH (Austria)
LKR LEICHTMETALLKOMPETENZZENTRUM RANSHOFEN GMBH (Austria)
For more information, please contact:
Denis Krajnc Project Coordinator
Mobile: +43 (0) 664-60885-953
Email: denis.krajnc@profactor.at
Website: www.compass-horizon.eu

Book chapter by Helmholz-Centrum Hereon and Wroclaw University of Science and Technology
SURE2COAT´s project parners, HEREON and WUST, published at the beginning of 2024 a chapter in a new book with the title «Advanced Ceramic Coatings for Energy Applications». It is a publication very related with the work the research institute and the university are doing within SURE2COAT. The book chapter abstract can be read here: Advanced Ceramic Coatings for Energy Applications - 1st Edition | Elsevier Shop.
"This chapter focuses on anticorrosive protective coatings on Al-based elements of thermal energy storage (TES) units working with phase change materials (PCM). The main challenges of such heat accumulators were discussed, highlighting especially their main drawback, which is low thermal conductivity. This feature impairs the charging and discharging rates and the overall efficiency of such storage tanks. An opportunity for solving this problem was presented – the immersion of spatial metallic structures in the PCM deposit that significantly facilitate heat transfer. Nevertheless, working in an aggressive environment of molten salts as PCMs requires additional protection of the metal surface against corrosion.
While giving a brief overview of various protection methods, this work primarily evaluates the utilization of plasma electrolytic oxidation (PEO) oxide layers for this purpose. It characterizes PEO coatings for aluminum substrates in details and suggests the possible strategies to further improve the performance of these layers in TES applications."

New technology redefines energy efficiency (article)
A EU project is dedicated to advancing energy efficiency through the development of innovative and eco-friendly corrosion protection methods, with the goal of replacing steel with aluminum.
SINTEF coordinates the SURE2COATproject, which stands for "Sustainable Surface Treatments of Complex Shape Components for Transsectorial Industrial Innovation." The project aims to raise the level of surface treatment methods from research to practical application in industry.
The main goal of the project is to address challenges related to corrosion of aluminium alloys in given environments and improve the effect of “gas-water heaters" where the heat-conducting parts of copper may be covered with a water film that reduces heat transfer.
In three very different applications, the project will demonstrate the new production concepts and demonstrate increased sustainability for the entire production, use and reuse chain of aluminium and copper. We want to address the challenges in the following three applications:
- Motor housing for the food industry
- Macro capsules for heat storage
- Gas-water heaters
For the first two applications, the goal is to replace steel as a material with aluminium alloys, while for the copper-based unit (gas-water heaters) we want to change the structure of the surface using laser.
To ensure relevance and efficiency, the project has partnered up with four industry partners, tnamely SIEMENS, BOSCH, MicroArc and COWA. These partners cover each of the three applications, and their insight and expertise will be critical to realising the project's objectives.
What surface treatment methods are we talking about?
- Sustainable aluminium: SURE2COAT is exploring methods such as plasma electrolytic oxidation (PEO) to create corrosion-resistant surfaces on aluminum alloys. This can replace steel in many applications and significantly reduce its weight, while improving durability and reducing energy consumption.
- Hybrid materials: Using techniques such as stainless steel spray coating, your product can achieve the best of both worlds. This means preserving aluminium's light weight and good thermal conductivity while using steel's corrosion resistance. This is especially important for the food industry and other sectors with strict standards.
- Laser precision: SURE2COAT will apply laser structuring techniques to alter copper surfaces at the micrometer level. This optimizes heat transfer and reduces water condensation in gas-water heaters.
The importance of sustainability and climate friendliness
SURE2COAT aims to raise the status of the three coating methods from TRL 3 to TRL 6 (Technology Readiness Level). This involves validating that the methods provide adequate corrosion protection, are environmentally friendly and can be integrated into production processes with reduced energy consumption and environmental impact. This initiative represents:
- New green surface treatment: SURE2COAT seeks to establish sustainable surface treatment methods that will have a positive impact on both the environment and energy consumption.
- Industrial transformation: By integrating these methods into production processes, the project contributes to a reduction in environmental impact and energy consumption compared to existing technologies.
- Commercial use: Upon reaching TRL 6, SURE2COAT are approaching commercial use, and the results have the potential to change industries worldwide

Manufacturing of Complex shapes, practical Workshop at WUST, May 15-19, 2023
From the 15th to 19th of May, 2023, Wrocław University of Science and Technology (WUST) hosted a workshop in which Sure2Coat partners could delve into the details of manufacturing complex shapes via investment casting technology.
The participants started with a 3D modeling course during which they designed spatial structures. Further days were packed with preparing models, molds, and casting. Additionally, the partners visited MicroArc company, where PEO coatings for proposed solutions in the project will be applied. They also visited the project partner MicroArc.
See pictures in Workshop WUST.

Sure2Coat is proud to have two new partners: POLIMI and Avio Aero
The new partners are Politecnico di Milano and Avio Aero. They joined consortium in the 2nd trimester of 2024 and will work on a use case related to surface treatment of aluminium parts using cold spray technology.

Research on Latent Heat Storage (LHS) challenges in Phase Change Materials (PCM) presented in EUROCORR 2024
Daniel Blücher, Håvard Wilson, John Erik Lein from SINTEF and Poppy O’Neill from COWA Thermal Solutions showcased the latest Sure2Coat findings on Latent Heat Storage (LHS) challenges in Phase Change Materials (PCM) at EUROCORR 2024 conference on September 4th in Paris, France. The project is pioneering the uptake of aluminium alloys in new sectors involving products with complex shapes, by new sustainable manufacturing methods with lower energy consumption for end users.

Check the video describing the R&D work by the University of Aveiro team and Bosch Portugal
See the video where you can know more about the work which is being done by the University of Aveiro and Bosch Portugal within the framework of SURE2COAT, in close collaboration with the rest of project beneficiaries. Just click on the following link: Optimising laser-based surface treatments to boost heat exchangers in gas water heaters.

CIDETEC Surface Engineering hosted in April 2024 the Surface Treatments Pilot Lines workshop in San Sebastian
The event, organised by the Sure2Coat project and the collaboration of the Bilasurf project, featured the presentations of first-class experts, from leading companies, centres and universities such as Siemens AG, Elsyca, Helmholtz-Zentrum Hereon, Micro-Arc S.C., University of Aveiro and CEIT.
During the two days, attendants visited the adjacent facilities of CEIT and CIDETEC Surface Engineering, both located in San Sebastian, Spain, with various pilot plants for scaling different surface treatments, where live demonstrations were held.

SURE2COAT in ManuDays 2024 (Brussels, May, 2024)
𝐓𝐡𝐞 𝐌𝐚𝐧𝐮𝐟𝐚𝐜𝐭𝐮𝐫𝐢𝐧𝐠 𝐏𝐚𝐫𝐭𝐧𝐞𝐫𝐬𝐡𝐢𝐩 𝐃𝐚𝐲𝐬 𝟐𝟎𝟐𝟒, organised by EFFRA in Brussels on May 7th and 8th, was an ideal opportunity to network with other Horizon Europe and Horizon2020 manufacturing projects, and to showcase Sure2Coat alongside two of our sister projects, FABulous Project and BILASURF, who are also advancing research in products with complex functional surfaces.
CIDETEC Surface Engineering and SUPSI were there representing Sure2Coat and it was useful to be able to share discussions and experiences with our sister projects.

Sure2Coat updated its website with description and links to its EU sister projects.
SURE2COAT works transsectorial to develop new sustainable surface treatments for the future European manufacturing ecosystems. Its sister projects BILASURF, FABulous Project, SYNTECS Project and CLASCO are all under the same work programme and topic and will together impact the development of new products with complex functional surfaces. The projects are funded by the European Commission. Visit the web site of SURE2COAT to learn more.
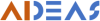
AIDEAS 3rd Newsletter
In the 3rd AIDEAS Newsletter, we are pleased to present our new YouTube video outlining the project's objectives, details of our second technical review, in which we showed demonstrations to the project officer and highlights from our plenary meeting at the Madeira Digital Transformation Week. The campaign to select participants for the Early Adopters Programme has been successfully completed, with many equipment manufacturing companies applying to benefit from using AI in their processes. We will also present the latest congresses in which we have participated, sharing the advances of the AIDEAS project, as well as handing out our dissemination material, such as the Magic Cube. Finally, we present the latest publications on AIDEAS initiatives published in scientific journals.
You can check the 3rd AIDEAS Newsletter here: https://mailchi.mp/789acd97b7a2/aideas-newsletter3
New YouTube video is available here: https://www.youtube.com/watch?v=OE26uiwxTu4
Stay tuned to dive deeper into our journey and celebrate our continuous progress and success.
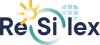
Recycling materials for PV and Battery valuechains: 2 years of progress
After 2 years since the proect start, in June 2022, Resilex partners have achieved significant results in the course of their activities. The following Newsletter summarizes those results, providing detailled insights on the following items:
- Recovering Mine waste
- Sustainable Silicon production
- Sustainable, eco-designed solar cells & modules
- Silicon recycling from PV modules
- Silicon composite for Li-ion batteries
- Impact assessment and Policy
- The Brussels workshop
You can download the Newsletter HERE

Engineered Wood Products: What’s the Way Forward? – NewWave Webinar #2
The term “engineered wood” refers to a wide range of wood products that are essentially made by wood derivatives (fibers, particles, strands, etc.) put together with adhesives or other fixation techniques. It has wide applications in the construction and furniture industries.
In NewWave, the partner FORESA Tech will use the lignin extracted from the Fast Pyrolysis Oil (FPBO) as a replacement for fossil phenol in a variety of existing resin formulations. In this webinar, taking place on the 4th of September (11:00 AM – CET) Luis Alberto Otero Vazquez (FORESA Tech) will present the following items:
- Overview of the engineered wood sector and current modes of production (and sustainability issues)
- What is the NewWave concept in this sector
- Achievements so far and future steps of the NewWave value chains

Two years of achievement in advancing Sustainable materials
More than 2 years have passed since the start of the NewWave project and several concrete results have already emerged from the Manufacturing lines as well as the complementary activities.
In this Newsletter we summarize the main results of the first two years of activities. The updates mainly refer to the materials developed in the Manufacturing Lines, the waste water treatment and the activities of the BIO-MATTERS cluster
HERE you can download the document.
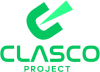
Official CLASCO Project Video released
We are delighted to present the official CLASCO project video, which provides an in-depth insight into our innovative journey.
This video briefly introduces our partners and outlines the motivation and objectives of the CLASCO project and is divided into key sections:
- Introduction: Examines the traditional production of complex parts and its limitations.
- Project overview: Andrés Lasagni, the project coordinator from the Technical University of Dresden, gives a general overview of the CLASCO project.
- Optimised designs through additive manufacturing: Presents weight reduction through optimised design and additive manufacturing processes.
- Polishing and surface functionalisation: Demonstrates the laser-based polishing process with microscope images and expert commentary from Thomas Burry, the CEO of SYLAS.
- In-line monitoring: Highlights the use of infrared cameras and plasma sensors for real-time monitoring.
- AI and Machine Learning Integration: Describes the AI solutions integrated into the CLASCO machine.
- Use Cases: Presents five real-world use cases from consortium members.
- Sustainability Assessments: Includes insights on sustainability from Gesa Beck, CEO of ABCircular.
The CLASCO machine and its components are explained in detail, demonstrating the highlight of our collaborative efforts. Consortium members and interviews play a crucial role in narrating this journey, providing a full understanding of the impact and innovation of the project.
Our consortium includes: ABCircular GmbH, Airbus Defence and Space, CATEC, CT Ingenieros A.A.I. S.L., DePuy Synthes, German Society for Materials Science (DGM), New Infrared Technologies (NIT), nLIGHT plasmo, Steinbeis Europa Zentrum, SurFunctionGmbH, SYLAS, Technische Universität Dresden, Z Prime.
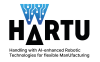
Free webinar on soft grippers: the HARTU project
📣 📅 Mark your calendars for HARTU's 1st online #webinar titled "How to pick (almost) anything: soft-grippers revolution", on February 14th 2024.
Take part of #HARTU research progress and learn more about our versatile soft grippers, developed by our partners Omnigrasp and Politecnico di Bari.
👉 Register now: https://docs.google.com/forms/d/e/1FAIpQLSeWWdBa3UCW8vbu8HceYymdNW3Es87iztXEK3sCVDcQUaJXFA/viewform
🔗 The agenda is available here: https://www.hartu-project.eu/2024/01/30/1st-hartu-webinar/
#Manufacturing #Robotics #AI #SoftGrippers #Innovation
Project Closed Successfully! Check out the key outcomes!
Our RECLAIM project has officially reached its end and was closed successfully.
A big thank you to every team member for your hard work, dedication, and collaboration. This success is a result of our collective efforts, and I'm confident that the skills and camaraderie built during this project will launch us to new heights in the future.
After all, our journey doesn't end here. In fact, it's a transition to a new phase where we leverage the insights gained to foster circular economy in manufacturing.
We encourage you to check out the main outcomes here: RECLAIM - Refurbishment and re-manufacturing of large industrial equipment (reclaim-project.eu)
Feel free to reach out to us and connect, to build on the achievements in RECLAIM.
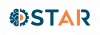
MARKET by STAR: the insights on the current trends, success stories and future developments related to Safe and Trusted Human-Centric Artificial Intelligence in Manufacturing
With the growth and improvement of production automation in manufacturing, Artificial Intelligence (AI) systems must be safe, trusted, and secure, even when operating in dynamic, unstructured and unpredictable environments. In this regard, one of the STAR project goals is to research and make available new technologies to enable standard-based, secure, safe, reliable and trusted human-centric AI systems in manufacturing environments.
MARKET by STAR is the entry point where all the interested visitors can consult the information representing the results of the project at one place along with the broad range of additional resources and services related to trustworthy Artificial Intelligence in manufacturing.
Visit MARKET by STAR: https://www.market.star-ai.eu/
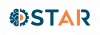
“Trusted Artificial Intelligence in Manufacturing”STARs Open Access Book reaches more than 40.000 downloads
The STAR Open Access Book “Trusted Artificial Intelligence in Manufacturing” reached more than 40.000 downloads.
This book is co-authored by the STAR consortium members and provides a review of technologies, techniques and systems for trusted, ethical, and secure AI in manufacturing.
The different chapters of the book cover systems and technologies for industrial data reliability, responsible and transparent artificial intelligence systems, human centered manufacturing systems such as human-centred digital twins, cyber-defence in AI systems, simulated reality systems, human robot collaboration systems, as well as automated mobile robots for manufacturing environments.
Check out our Open Access Book and other publications at https://star-ai.eu/publications.
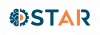
STAR Results in Brief article published on CORDIS!
We are excited to announce that the STAR Results in Brief article has been published under the Results Pack on human-centric manufacturing on the CORDIS website at:
https://cordis.europa.eu/article/id/445276?WT.mc_id=exp
The article, titled "People-first approach helps build trust in manufacturing AI" is provided in six languages (DE, EN, ES, FR, IT, PL). It explains how the STAR project uses human-centric design to build safe and reliable technologies. It explains the risks and challenges in enhancing the intelligence of manufacturing processes and the benefits of trust-building AI systems. The article focuses on the novel AI technologies evaluated and validated in three pilots for both technical and social performance – in particular, their trustworthiness.
Enjoy reading!
The full Results Pack can be found here:
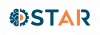
STAR at the EFFRA Manufacturing Partnership Day
STAR participated in The Manufacturing Partnership Day, which took place on the 26th of September 2023 in Brussels. The event co-organised by the European Factories of the Future Research Association (EFFRA), and Factories of the Future and Made in Europe projects brought together the Factories of the Future and Made in Europe community and showcased ongoing projects' work.
It was a rich day full of stimulating presentations and exchanges, where participants had the possibility to learn more about Made in Europe and Factories of the Future projects and network with like-minded manufacturing innovation and research professionals.
STAR showcased the state of play of the project with a presentation made by the project Technical manager Dr.John Soldatos (Netcompany-Intrasoft) and displayed its new 8-page brochure featuring the project's results and the STAR book at a stand in the event's exhibition. Visitors to the stand had the possibility to discuss with the STAR experts the latest project developments and the general state-of-the-art in the field of AI in manufacturing.
The STAR video shown at the event is available on our YouTube channel: https://www.youtube.com/watch?v=lhNB5I6KYjw
More information about the event is available at https://effra.glueup.com/event/the-manufacturing-partnership-day-76855/
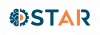
STAR presented at IFAC 2023, Yokohama, Japan!
During an exciting week in Yokohama, Japan at the triennial IFAC World Congress 2023, STAR partners had the opportunity to present and discuss significant contributions of the project in addressing the pertinent issues of human-centric AI in manufacturing.
- How to assess human centricity of AI-driven industrial systems?
https://lnkd.in/dJUfmRu3
- How can robots in shared human-robot spaces anticipate human movement for safer and efficient co-existence?
https://lnkd.in/d7j7pFEt
- How can we involve the human in the AI loop during visual quality control and what this means for changing job profiles, shifting workers to more cognitively demanding tasks?
https://lnkd.in/dJQaFWCE
These are based on a collaborative work between our partners: the University of Groningen, the Jozef Stefan Institute, QLector, Thales, and the University of Applied Sciences and Arts of Southern Switzerland.
The IFAC World Congress is the largest event in the field of control science and technology, held every three years. It offers the most up-to-date and complete view of control techniques, with the widest coverage of application fields, and is attended by a worldwide audience of scientists and engineers from academia and industry. This year's Congress took place on 9-14 July 2023 in Yokohama, Japan.
More info about the event is available at https://www.ifac2023.org/
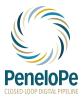
WORKER-CENTRIC TOOLS ASSISTING IN THE EXECUTION OF THE LABOUR-INTENSIVE TASKS BOOKLET
Penelope is a new Industry 4.0 solution to further innovation in intelligent, efficient and flexible manufacturing for high-precision large parts.
The project, supported by the European Commission and launched in November 2020, is taking advantage of the new horizons in manufacturing, opened by Industry 4.0, to develop a novel closed-loop digital pipeline based on the development of modular and reconfigurable production approach for the manufacturing of high-precision large-scale parts.
Together and for a period of 48 months, PENELOPE´s extensive and multinational partnership of 31 European organizations, led by AIMEN TECHNOLOGY CENTRE, is developing an end-to-end digital manufacturing solution for a flexible and more precise manufacturing of large-parts in novel connected factories. PENELOPE relies on a modular, flexible and worker-centric approach, targeting key labour-intensive and non-ergonomic tasks while preserving workers’ knowledge and skills. Penelope´s solution will allow factories to release highly customised and value-added products while reducing reconfiguration time.
This booklet is the outcome of three PeneloPe deliverables:
- Safe, modular and flexible robotics technologies showcasing pre-pilot demonstrators for flexible and safe collaborative robots operating in large-part high-precision manufacturing applications led by COMAU with the collaboration of the project partners Airborne, LMS, TECNALIA, JASO, UNIMORE, K-Loops, Fraunhofer IGP, AIMEN, DGH, TNO, TU Delft, SAMXL and the University of Coimbra.
- Intuitive human-robot collaborative solutions showcasing pre-pilot demonstrators featuring HRI/C at both cognitive and physical level led by LMS with the collaboration of the project partners AIMEN, TECNALIA, DGH and the University of Coimbra.
- AR/VR tools showcasing the AR/VR tools assisting in manufacturing, supervision and in-situ repair led by TTPSC, with the collaboration of other project partners LMS, BIBA, CEA List and IPC.
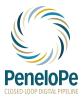
PeneloPe’ Demonstrator, VDL Bus & Coach, wins prestigious ‘Red Dot’ again for design of the new generation Citea
The jury of the world’s most prestigious design competition, Red Dot, gave the award in the ‘Product Design’ category to the new generation Citea. The electric buses from VDL Bus & Coach are entirely based on an electric drive train and have
trend-setting features. The jury praised the “high design quality and excellent
design”.
The Red Dot Award has been awarded annually in several categories since 1955 by the Design Zentrum Nordrhein Westfalen in Essen, Germany. This year, the organisation had a record number of entries. The Red Dot Award for the new Citea generation will be presented on 20 June. “The fact that VDL emerged as the victor from such a strong group of participants is testament to the exceptional quality of the product,” judged Professor Dr Peter Zec, founder and CEO of the Red Dot Award. “In an evaluation process lasting several days, the entries from all over the world were examined in detail and assessed by experts for their design quality and degree of innovation.”
👉 Download here the Press Release: EN—Press-release-Red-Dot-Award-2022-for-design-new-generation-VDL-Citea.pdf
From PeneloPe we couldn’t be prouder! Congratulations to the VDL Bus & Coach Team for this tremendous acomplishment!
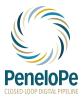
The New 4ZDM Website is LIVE!
This new online platform is the the European Home for Zero Defect Manufacturing.
The 4ZDM Cluster is a European initative around the Factories of the Future Zero Defect Manufacturing priority that aims to promote the adoption of zero-defect production and quality control systems by the industry.
This is a initiative launched by the European Projects: PeneloPe, OPTIMAI, i4Q, Data4Zero and InterQ.
Take a look at the 4ZDM website here: https://zdmanufuture.org/
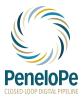
VDL Bus & Coach, PeneloPe’s Partner, wins iF Design Award
On 13 April 2022, after the prestigious Red Dot Award, VDL Bus & Coach, PeneloPe’s Partner has won another important design prize: the jury of the iF Design Award has honoured the new generation Citea with an award in the category ‘Product automobiles/vehicles)’.
The iF Design Award was introduced in 1954 and is awarded annually by the iF International Forum Design. This year there was a record number of entrants: 10,776 products and projects were eligible for an award. Winners include big names such
as Porsche, BMW Group and Sony. Red Dot and iF are widely regarded as the most important design awards in the world. From the jury rapport of the iF Design Awards 2022: “A scalable, sustainable solution for cities transitioning to net-zero. Innovations like a single piece of curved composite framing not only cut weight but create a more open, inviting interior. Developed alongside the most important drivers associations, the driver cabin also sets new standards for ergonomics, steering adjustments and dashboard space.”
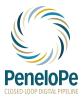
PeneloPe at FAIM 2023: PeneloPe wins the best extended paper and presentation!
Penelope Coordinator, AIMEN, and the PeneloPe Parners Fraunhofer IGP, ESI, UNIMORE, Universidade de Coimbra and ATOS have participated in the FAIM2023 International Conference that took place on June 18-22, 2023.
The Flexible Automation and Intelligent Manufacturing International Conference series has been run in 26 cities in 14 countries in Europe, America, and Asia, addressing both technology and management aspects. The 32nd FAIM International Conference, FAIM2023, is the milestone of 32 years of continuous presence in the international manufacturing scene. It also signifies a landmark in the Conference’s steering, organizational and scientific standards.
FAIM2023 was hosted by Polytechnic Institute of Porto, together with other Universities of the North of Portugal, whose are the main support for research and development of the industry sector mainly located in the North of Portugal.
The theme of FAIM2023 was establishing bridges for more sustainable manufacturing systems.
PeneloPe was featured through different actions during the event:
- PeneloPe won the best extended paper and presentation! The paper from UNIMORE was titled: ‘A method for the assessment and compensation of positioning errors in industrial robots’. Authors (CONGRATULATIONS!) Sergio Ferranini, Pietro Bilancia, Margherita Peruzzini and Marcello Pellicciari.
- Fraunhofer IGP also presented a paper on ‘Automation of Fitting Pipe Manufacturing in Shipbuilding’ whose authors are Klara Pejić, Konstantin von Haugwitz, Martin-Christoph Wanner and Wilko Flügge.
- Marcello Pellicciari from UNIMORE had the pleasure to present a keynote speech in which he will also talked about penelope.
- And last, but not least, Félix Vidal from Aimen presented a conference paper at the special session managed by Pedro Neto from Universidade de Coimbra on ‘Flexible and modular robotic manufacturing of large component‘. The authors of the paper were Félix Vidal from AIMEN and PeneloPe project coordinator, Lucía Alonso from AIMEN, Patrick de Luca from ESI Group and Roberto Castillo from ATOS Spain.
- Learn more about the event here: https://www.faimconference.org/
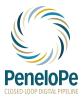
Penelope, proud member of the Horizon Results Booster
Horizon Results Booster (HRB) is an initiative of the European Commission, which aims to bring a continual stream of innovation to the market and maximize the impact of publicly funded research within the EU.
The Horizon Results Booster (HRB), is making waves in the world of innovation and research as it brings forth a continuous stream of groundbreaking technologies to the market while maximizing the impact of public-funded research within the EU. Among the standout participants in this prestigious program are Penelope, Optimai, and I4Q, who have been active members since March 2023 and have been reaping the benefits of various services, particularly in Dissemination and Exploitation Strategy.
One of the crucial services provided to these exceptional projects by the Horizon Results Booster has been strategic Dissemination and Exploitation. This support has allowed Penelope, Optimai, and I4Q to effectively communicate their groundbreaking research, technologies, and cluster initiatives to a wider audience, including potential investors, industry partners, and stakeholders.
Notably, the 4ZDM cluster, championed by the collaborative efforts of Penelope, Optimai, and I4Q, has emerged as a standout project within the Horizon Results Booster program. This transformative cluster initiative is a highly technology intensive and strategic manufacturing approach. The Dissemination services offered by HRB have been instrumental in highlighting the significance and potential of the 4ZDM cluster, garnering attention from industry leaders and reinforcing its position as a game-changer in the manufacturing sector.
The journey of Penelope, Optimai, and I4Q within the Horizon Results Booster is only just beginning and will help these projects develop and achieve great goals.
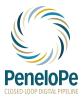
Be part of the Manufacturing revolution, Join the Penelope Community!
Are you passionate about cutting-edge advancements in manufacturing? Excited to be part of a dynamic community that’s shaping the future of precision engineering? Look no further! and join the PENELOPE online community!
PENELOPE stands for Precision Engineering for Novel and Enhanced Large Optics Production Ecosystem. The mission is to develop a unique closed-loop digital pipeline that’s founded on modular and reconfigurable production techniques.
As a member of the PENELOPE community, you’ll be at the forefront of manufacturing excellence and can access the following:
- News and Updates: Stay up to date with the latest developments in Industry 4.0, digital manufacturing, cutting-edge technologies and much more.
- Events: Participate in webinars, workshops, and virtual conferences led by industry experts and thought leaders.
- Insightful Articles: Dive deep into articles, research papers, and case studies that showcase the impact of modular production approaches and digital pipelines in the manufacturing realm.
- Discussions: Connect with fellow enthusiasts, professionals, and innovators in the manufacturing industry. Share your insights, learn from others, and engage in meaningful conversations.
- Networking Opportunities: Build valuable relationships with individuals who are shaping the future of precision engineering.
Join today and be part of the manufacturing revolution in Europe!
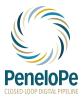
Safe the future with manufacturing innovation!
The ESCAPE ROOM where you will get hands-on experience on Industry 4.0 while playing with your friends.
In this online escape room, you will be cracking a code to unlock a message from the future by solving puzzles and challenges related to the world of advanced manufacturing and Industry 4.0.
You and 2 friends (connected through a common platform e.g. Zoom) must use your knowledge and skills to find clues to crack the code and save humanity.
Play now here: 👉 http://bit.ly/3IDEcXF
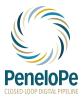
PENELOPE is featured in the EU Valorisation Week as a best practice
The EU Valorization Week held in 25-28 April 2023 provided professionals with a unique platform to exchange experiences, explore methodologies, and foster peer learning focused on sustainability, intellectual asset management, and industry-academia cooperation. The event aimed to facilitate networking, trend exploration, and the sharing of expertise, ultimately fostering collaboration and shaping the future of sustainable development and collaborative ventures.
PENELOPE is a European project that develops a novel closed-loop digital pipeline based on the development of modular and reconfigurable production approach for the manufacturing of high-precision large-scale parts. The project’s outstanding achievements led to its feature on the EU Valorization Week webpage as a Success Story, symbolizing the acknowledgment of the consortium profound knowledge and expertise in the domains of research and innovation.
The inclusion of PENELOPE in the EU Valorization Week webpage reflects the project’s status as a leading force within this esteemed forum, showcasing it’s remarkable progress in research and innovation. It also underscores its potential for transformative change that lies within the intersection of collaboration, sustainability, and intellectual asset management
To discover this PENELOPE’s Success Story click HERE.
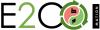
E2COMATION @hub.berlin 28-29th June
📣 Exciting opportunities await at the upcoming hub.berlin on June 28-29. E2COMATION is proud to invite you to join our masterclass🎓, held on June 28 from 14:00 to 15:30, where we delve into the critical theme: "Optimizing Energy and Resources for Modern Manufacturing".
This interactive session will be led by esteemed speakers from STIIMA-CNR, ACTOR, Kastamonu Entegre, Software AG, and Athens Technology Center, and KU Leuven. They will share their insights and the latest breakthroughs in energy efficiency and sustainable manufacturing processes.
Also, remember to visit our booth on both days of the event for an up-close look at our work towards making manufacturing more sustainable.
Visit https://e2comation.eu for more info, and we look forward to seeing you there!
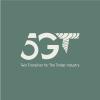
5G-TIMBER consortium meeting in Finland
In order to review the status and future plans for the 5G-TIMBER project, a group of top academic universities and industrial partners met in Espoo, Finland, from January 18 to 20, hosted by VTT. The meeting sought to give participants a forum to discuss ideas and best practices while also evaluating the general state of the project's activities.
Muhammad Mahtab Alam, the project coordinator for 5G-TIMBER, provided a status report at the beginning of the meeting, outlining the deliverables that had been submitted and upcoming, as well as milestones and overall thoughts on how the project was progressing. A rich discussion regarding the project's use cases followed, with the goal of ensuring that all pertinent partners were on the same page and that the necessary technological resources were assembled to put them into practice.
The project use cases:
-
UC1 - Data-driven sawmill and woodworking machine setup
This category addresses the first part of the value chain of the wood after forestry, starting from the cutting of the logs to their processing in sawmills to obtain lumber.
The focus of this category is on the equipment used in sawmills, specifically on the development, modernisation, setup, monitoring, remote operation and maintenance.
-
UC2 - Modular wood-house factory
This category addresses the use of wood parts in constructing modular pre-assembled modules of wooden buildings. The focus is on both the production site where the modules are assembled (i.e. the factory) and the module components. Modern technologies will be integrated into the production process to improve assembly efficiency, safety and integration with the product lifecycle management tools.
-
UC3 - Construction and renovation with wooden elements, valorisation of composite waste
This category covers the remaining part of the life cycle of a wooden house, namely the building at the specific site and the monitoring during the use phase. The end-of-life is focused on wooden composites wastes generated during the service life of the modules.
The project partners also had the opportunity to tour VTT's facilities in the afternoon, specifically the materials performance labs.
The second day was devoted to talking about various technological aspects. The project partners made sure that the technology solutions to be used in the use cases are appropriate and knew how to deploy them based on the individual partners' varying types and levels of competence and the unique characteristics of each pilot site. The consortium concentrated on commercialization and communication issues in the late afternoon; to find the people who can contribute to the project or are interested in its outcomes, a stakeholder mapping workshop was held.
On the third day of the meeting, the consortium started getting ready for the technical review meeting that will take place in May 2023. Most attendees left the meeting after that, and the Project Management Board members held a last meeting to go over next tasks and deliverables.
This project consortium meeting was a crucial turning point and a great chance to assess the project's overall development. Exciting activities and project work will occupy the upcoming months. To stay up to date with everything 5G-TIMBER, subscribe to our channels.
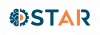
MARKET by STAR is now available!
Discover trusted Artificial Intelligence (AI) solutions in Manufacturing Lines at MARKET by STAR (https://www.market.star-ai.eu).
Register to access all available content (Success Stories, Assets, Training, and External AI Resources):
1) Visit the Success Stories of three Pilots sites focused on different areas of production and research:
- PHILIPS (Netherlands): Human-cobot collaboration for robust quality inspections;
- DFKI (Germany): Human behaviour prediction and safe zone detection;
- IBER OLEFF (Portugal): Human-centred AI for agile manufacturing 4.0.
The Success Stories are Experiences in real-world scenarios. Each one was characterised according to Value Propositions and ICT Problems. In addition, more information is provided, such as where and how it happened. The Value Propositions and ICT Problems were mapped with the Technologies (Assets) developed in the Project, allowing to perceive which Assets were used in the solutions and which ICT Problems they helped to solve.
2) Discover the Assets that support the implementation of trusted AI solutions in production lines. The Assets address different dimensions and elements of trust, security and safety in the operation of Cyber Physical Production Systems (CPPS).
3) Explore the Training Resources, courses, and workshops in the AI domain, as well as External AI Resources and external platforms with AI resources.
During the Project, new content will be added and other evolved.
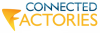
The ConnectedFactories Final Newsletter is out
As the ConnectedFactories project has come to an end in November 2022, we are pleased to present you the final newsletter, where you can find information and resources about the latest events.
- Business and Legal Online Workshop
- AI Pathway Workshop
- Foresight Workshop
- Connected Factories Final Event
Success driven by standardisation - register to this free webinar on 20 July
A crucial factor in innovation and collaborative work is an agreement on understandable and implementable standards.
On 20 July, you will learn about this in an exciting, free webinar organised by the European initiative ForeSEE and UNI. The main objective of the cluster is to create a roadmap for predictive maintenance, which may serve as a guideline for companies that want to adapt and adopt predictive maintenance solutions in the future.
Register now! Register here!
As part of the cluster, our H2020 project RECLAIM intends to demonstrate strategies and technologies that enable the re-use of industrial equipment in old, renewed and new factories alike. Learn more in our website and get in touch with us! RECLAIM - Refurbishment and re-manufacturing of large industrial equipment
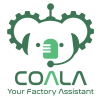
COALA Newsletter #3 - Intelligent Cognitive Assistance for Liquid Production Line
Welcome to the 3rd edition of the COALA Newsletter. A key milestone has been reached with the release of the second prototype of the COALA main components. These trustworthy AI components with a voice-enabled Digital Intelligent Assistant as an interface have been integrated and will be evaluated within the coming months in the three business cases. This achievement was recently presented at the project‘s mid-term review, which took place successfully in the beginning of May 2022.
This newsletter edition will highlight the implementation of one of COALA's AI components, Cognitive Advisor Service, within the DIVERSEY business case in order to support line operators and managers towards optimum configuration of the production line.
COALA partners have been active also in dissemination and community management activities. COALA has organised its first webinar on 20th of May 2022, where we introduced some benefits of application of Digital Intelligent Assistants in the quality testing of white good use case and showed a demo on the current prototype of the Augmented Manufacturing Analytics feature. A recording of the webinar is available here.
In the community and event sections of this newsletter, you will find some of the past and upcoming event highlights. We hope that you will find our newsletter interesting and useful. If you have suggestions for future topics this newsletter should cover, do not hesitate to contact us.
Enjoy reading our newsletter!
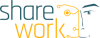
EVENT 07/07/2022 - COLLABORATIVE ROBOTICS’ INDUSTRIAL IMPLEMENTATION: TOWARDS MORE FLEXIBLE AND INTEGRATED WORKPLACES
REGISTER: https://cutt.ly/ShareworkHRCImplementation
10.00 – 12.15h CEST
Human-Robot Collaboration is a key factor in the field of industrial robotics for the development of the factories of the future and advance towards the Industry 4.0 paradigm.
In this last training session of the Sharework project we will introduce some basic concepts of the implementation of Human-Robot Collaborative systems and the advantages of its wide deployment into the industry. In addition, four use cases implemented in four companies in the transport, capital goods and metal sector will be presented, highlighting the potential of collaborative robotics in operators’ ergonomics and wellbeing, as well as the benefits from the production side.
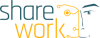
EVENT 20/06/2022 - ROBOT AND HUMAN MOTION PLANNING IN COLLABORATIVE ROBOTICS
REGISTER: https://cutt.ly/ShareworkMotionPlanning
20/06/2022
14.00 - 16:00 PM
Robot and human path planning is essential for the implementation of accurate, safe and effective Human-Robot Collaboration (HRC) systems, making sure to avoid incidents in the workplace, as well as increase productivity and work quality thanks to the collaboration between workers and robots.
In this training session on motion planning in Human-Robot Collaboration of the Sharework project, we will review state-of-the-art approaches for robot planning and scheduling, and present advances in the field with great potential to contribute to a widespread uptake of high-payload collaborative industrial robots in assembly shopfloors. As part of the training activity, a hierarchical motion planning framework to plan and execute human-aware movements and research on human motion prediction applicable into robot motion planning will be presented.
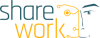
EVENT 05/05 - HUMAN FACTORS IN HUMAN-ROBOT COLLABORATION
REGISTRATION - https://www.tfaforms.com/4975826
AGENDA AND MORE INFORMATION - https://sharework-project.eu/events/sharework-training-activity-2-human-factors/
In recent years, manufacturing aimed at increasing flexibility while maintaining productivity for satisfying emerging market needs for higher product customization. Human Robot Collaboration (HRC) is a promising way of achieving this balance by combining the improvisation and dexterity of humans with robots’ tireless precision and repeatability.
However, collaborative robotics developments have focused primarily on the technology and, until recently, little research has been geared to understand the key human factors that need to be considered to enable successful implementation of industrial HRC.
This training session, the second of a series of training workshops organized by the Sharework project, will be focused on Human Factor approaches in collaborative robotics from several perspectives. Contents of this session respond to how to develop a more human-centered design for the factory of the future, including ergonomic and posture assessments, methodologies to ensure adaptability and acceptance of collaborative robotics solutions in the workplace, the use of Augmented Reality for operator training and technology for a seamless interaction between humans and cobots.
CoLLaboratE project has been completed!
It was an incredible journey of 42 months with a lot of challenges. Fortunately, we managed to get through and we are proud to integrate our novel technologies in four use-cases that range from the electric apliance-, to the automotive-, and the aerospace- industries.
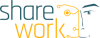
Training activity - MANUFACTURING ENVIRONMENT PERCEPTION FOR AN EFFECTIVE HUMAN-ROBOT COLLABORATION
06/04/2022 - ONLINE - 14.00 - 16.45PM
Registration: https://www.tfaforms.com/4969763
More information: https://sharework-project.eu/manufacturing-and-environment-perception-for-an-effective-human-robot-collaboration/
Autonomous and hybrid plants require a high level of automation and understanding of the processes within where collaborative robots have a high potential. The development of collaborative robotics as a research area is based on the study of computer vision, machine learning and artificial intelligence to provide robots with high vision skills and knowledge to interact safely and effectively in the workplace and assist humans in arduous or repetitive tasks.
In this training session, the first of a series of training workshops, several perception techniques to increase collaborative robots’ knowledge and skills to perceive, comprehend and reason about the surrounding environment will be presented. The concepts presented will include several technologies and methodologies to enhance the robot ability for the detection of the objects and humans in the environment, identify humans’ posture and activities and understand the human behavior or model desired motions for our robots.
During the session, showcasing basic concepts on methods to enrich collaborative robotics recognition and perception capabilities, Sharework researchers aim to contribute to training the next generation of Human-Robot Collaboration investigators and disseminating project advancements to the scientific and education community. The session content comprises basic concepts and techniques used to perform an environmental analysis and provide robots with the necessary intelligence to recognise their surroundings and act accordingly. The concepts presented are going to be exemplified with comprehensive case studies developed under the framework of the Sharework project.
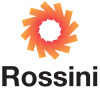
The Rossini project: platform’s integrations in use cases - OPEN WEBINAR
The final Open Webinar of the ROSSINI project will focus on the results achieved by the implementation of innovative solutions within the Collaborative Robotics field, in the 3 industrial Use Cases (IMA, WHIRLPOOL, SCHINDLER).
The webinar will be online, on March 23rd at 3 pm.
Please click on the link below and register!
https://www.crit-research.it/it/eventi/rossini-platform-integration-in-use-cases/

EU project makes headway in zero-defect manufacturing
- EU funded project introduces new Artificial Intelligence (AI) methods for improved quality in manufacturing
- The OPTIMAI project presents intelligent approach to zero-defect manufacturing through its breakthrough AI powered toolkit
- 16 partner organisations from 8 countries across Europe join forces to optimise production processes through a mix of AI, augmented reality, virtualisation and smart sensors
20th January 2022
Manufacturing industries are constantly looking for new ways to improve quality control for both manufactured products and manufacturing processes. The OPTIMAI project is spearheading innovation in this area. Introducing new technologies designed to reduce scrap, eliminate defects, maximise productivity and improve quality of shop floor processes, the project is set to make a tangible impact on European industry and environmental sustainability.
“We are effectively looking to create a new industry ecosystem. We are optimising production processes through a unique mix of Smart Instrumentation, Metrology, Artificial Intelligence, Virtualisation and Augmented Reality”, says OPTIMAI Project Coordinator, Dr. Nikolaos Dimitriou from the Centre for Research and Technology Hellas (CERTH-ITI).
The three-year project, funded by the European Commission’s Horizon 2020 research and innovation programme, is shaping the factories of the future thanks to its unique set of smart technology designed for the manufacturing arena. OPTIMAI was launched in January 2021 and has just entered its second year.
The manufacturing industry has spent the last few decades in a continuous state of technological revolution with the progressive introduction of ICT, robotics, and automation technologies and most recently the introduction of digitalisation technologies on the shop floor. OPTIMAI is now revolutionising current industry practices further by bringing together and advancing several enabling technologies that strengthen the collaboration between humans and machines.
Dr. Dimitriou and his team have designed the OPTIMAI toolkit, which will initially be tested and validated in factories focusing on the manufacturing of lifts and antennas and on the assembly of microelectronics in Greece, Spain and the UK respectively. The highly adaptable solutions will then be applied in a wide range of industrial settings and brought to market across Europe.
“We aim to strike an optimal balance between fast, cheap and reliable production choices that have a significant impact on industrial competitiveness.”, Dr. Dimitriou explains.
Core parts of the toolkit developed by contributing organisations include a decision support system that detects and issues early notifications of defects, a continuous production, monitoring and quality inspection system powered by smart sensors, an intelligent marketplace for recycling of scrap, digital twins for simulation and forecasting of industrial processes, and, of course, a comprehensive ethics and regulatory framework surrounding the technologies.
Feeding into the current transformative phase in the Industrial Revolution known as Industry 4.0., the project’s innovations go beyond the state of the art and pave the way for a smarter, digitalised European manufacturing domain.
Survey for machine / equipment / tools manufacturers & service providers: Impact of Remanufacturing/Refurbishment in the Sector
Help us understand if and how you perform remanufacturing/refurbishment!
RECLAIM – RE-manufaCturing and Refurbishment LArge Industrial equipment (EU H2020) – is conducting a survey with machine / equipment / tools manufacturers and service providers to analyse the elements of greatest relevance in remanufacturing/refurbishment strategies for companies of the electromechanical sector.
Take a few minutes to fill in our questionnaire here.
The collected data will be aggregated and used for a public report on how to support RECLAIM strategies for refurbishment and remanufacturing that enable the reuse of industrial equipment in old, renewed and new factories alike, addressing also themes such as valuable materials and the interaction with services and after sales functions.
Should you have any questions, or wish a digital copy of the public report once available, do not hesitate to contact Lucrezia Quarato, Project Manager at RECLAIM project partner SCM group.
Thanks a lot in advance for your support!
Remanufacturing or second-life production implies using parts of discarded products in a new product with the same function. Remanufactured products guarantee the same quality like original products, as they are brought at least to original equipment manufacturer performance specification.
Refurbishment means restoring an old product and bringing it up to date, in order to maintain reliability or extend service life. In general, refurbished products are upgraded and brought back to specified quality standards or satisfactory working and/or cosmetic conditions and have to fulfil extensive testing. Occasionally, refurbishment is combined with technology upgrading by replacing outdated modules and parts with technologically superior ones.
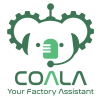
COALA Newsletter #2 - Solution and AI-assisted on-the-job training for textile workers
Dear Reader,
After 15 months, COALA is close to reaching its third milestone. It will have a second prototype and its components will be ready for integration into the three industrial business cases. This issue will present COALA's solution and its underlying components, as well as the introduction of the textile business case. This case focusses on training and development of textile worker's AI competencies.
COALA partners have been active also in dissemination and community management activities. The next event co-organised by COALA is the 4th International Workshop on Key Enabling Technologies for Digital Factories (Ket4DF) in conjunction with CAiSE 2022, which will be held on 6 – 10 June 2022 in Leuven, Belgium. More detailed information on the paper submission date is available on the Ket4DF 2022 website. In the community and event sections of this newsletter, you will find some of the past and upcoming event highlights.
We hope that you will find our newsletter interesting and useful. If you have suggestions for future topics this newsletter should cover, do not hesitate to contact us.
Enjoy reading our newsletter!
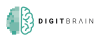
Open Call Announcement: Application Phase starts on February, 28th 10:00h (CET Time)
DIGITbrain - Second Open Call for Application Experiments
H2020 DIGITbrain project, funded by EC under the Grant Agreement number 952071, includes Financial Support to Third Parties (FSTP) under two Open Calls. DIGITbrain has the ambition to transform the CloudiFacturing Solution and ecosystem (developed in the H2020 CloudiFacturing Project) towards the requirements of Manufacturing as a Service (MaaS), utilising the Digital Brain and its underlying technology components as the main innovation of the project.
This Open Call is focused on attracting Third Parties (especially manufacturing and ISV SMEs and mid-caps) to perform experiments to validate the DIGITbrain solution and to make SMEs more competitive by transferring innovative solutions into the wider manufacturing community. Experiments will be implemented in close collaboration with Digital Innovation Hubs and technical partners of Competence Centers. This interaction should start during proposal preparation, with DIHs and technical partners of competence centers acting as business and technical supporters for applicants. This collaboration will then continue during the experiments’ deployment and execution.
Key Call Details
Project full name: Digital twins bringing agility and innovation to manufacturing SMEs, by empowering a network of DIHs with an integrated digital platform that enables Manufacturing as a Service (MaaS)
Project acronym: DIGITbrain
Call identifier: DIGITbrain – OC2
Project grant agreement number: 952071
Call opening: 28th February 2022, 10:00h (CET Time)
Submission Deadline: 31st May 2022, 17:00h (CEST Time)
Expected duration of participation in experiments: 12 months
Total EC funding available for Third Parties in DIGITbrain-OC2: up to 684.600 EUR financial support for Third Parties is available to support 7 experiments. DIGITbrain considers that proposals requesting a contribution up to 97,800 EUR per experiment would allow the specific challenge to be addressed appropriately. Nonetheless, this does not preclude submission and selection of proposals requesting other amounts.
Maximum amount of financial support for each Third Party: 60,000 EUR
Language in which proposal should be submitted: English
Weblink for further information (full call text/proposal guidelines/call results) on the official project website: https://digitbrain.eu
Email address for further information: opencall@digitbrain.eu
Expectations for Experiments
Grounding on the Digital Twin concept, experiments will be focused on enabling the customization of Industrial Products (intended as systems operated by manufacturing companies to support the production of the final consumer products) and facilitating cost-effective distributed and localised production for manufacturing SMEs or mid-caps, by leveraging edge, cloud and HPC-based modelling, simulation, optimisation, analysis, and machine learning tools. Experiments can cover any segments in the manufacturing sector at large, including (but not limited to) discrete manufacturing, continuous production, or construction.
Experiments should aim at covering the development and uptake of digital technologies especially in segments where these are underexploited.
An experiment consortium has to meet the following requirements:
- The minimum number of partners in an experiment consortium must include:
- One End User (mainly SMEs); and
- One Technical partner acting as Independent Software Vendor (ISV), engineering or software consultant.
- All Third Parties must come from European Member States, Associated Countries or the United Kingdom [1].
- According to the EC rules, no Third Party is allowed to have received more than 100,000 EUR from Horizon 2020 I4MS and SAE Open Calls [2].
[1] For further information, please visit: https://ec.europa.eu/info/research-and-innovation/statistics/framework-programme-facts-and-figures/horizon-2020-country-profiles_en
[2] DIGITbrain will receive assistance from the European Commission to cross-check if an organization that has been shortlisted for funding under the current DIGITbrain’s OC2 has already received FSTP via an Open Call under any other H2020 I4MS/ SAE Project and to ensure that the right funding is allocated to a Third Party in case it exceeds the above threshold (including any DIGITbrain potential funding).
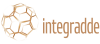
IEEE Access and INTEGRADDE invites manuscript submissions in the area of Metal Additive Manufacturing!
Submission Deadline: 30 November 2021
IEEE Access invites manuscript submissions in the area of Metal Additive Manufacturing.
Additive manufacturing (AM) is a main driver of the Industry 4.0 paradigm. While the additive manufacturing of plastics is common, metal additive manufacturing processes still face several research challenges. The high cost and unpredictable defects in final parts and products are preventing complete deployment and adoption of additive manufacturing in the metalworking industries. Several aspects need improvement, including robustness, stability, repeatability, speed and right-first-time manufacturing. Nevertheless, its potential to the production of structural parts is significant, from the medical to the aeronautics industry.
This Special Section in IEEE Access will bring together academia and industry to discuss technical challenges and recent results related to additive manufacturing. Theoretical, numerical and experimental development in this domain are welcome. The articles are expected to report original findings or innovative concepts featuring different topics related to metal additive manufacturing. Industry-related studies are welcome, especially the ones demonstrating advanced applications of metal additive manufacturing in challenging scenarios.
The topics of interest include, but are not limited to:
- Data interoperability
- Data analytics
- Digitalization and data security
- Topologic optimization
- Additive manufacturing building strategy
- Multi-physics process simulation and modeling
- Product engineering optimization
- Testing and characterization
- Zero defect manufacturing and process control
- Quality assurance
- From CAD design to real part production
- Advanced industry applications
We also highly recommend the submission of multimedia with each article as it significantly increases the visibility and downloads of articles.
Associate Editor: Pedro Neto, University of Coimbra, Portugal
Guest Editors:
- Mustafa Megahed, ESI Group, Germany
- Matthew Gilbert, The University of Sheffield, UK
- Kaixiang Peng, University of Science and Technology Beijing, China
- Felix Vidal, AIMEN Technology Centre, Spain
- Leroy Gardner, Imperial College London, UK
- Xuemin Chen, Texas Southern University, USA
- Stasha Lauria, Brunel University London, UK
Relevant IEEE Access Special Sections:
- Advanced Artificial Intelligence Technologies for Smart Manufacturing
- Key Technologies for Smart Factory of Industry 4.0
- Advances in Machine Learning and Cognitive Computing for Industry Applications
IEEE Access Editor-in-Chief: Prof. Derek Abbott, University of Adelaide
Article submission: Contact Associate Editor and submit manuscript to:
http://mc.manuscriptcentral.com/ieee-access
For inquiries regarding this Special Section, please contact: pedro.neto@dem.uc.pt.
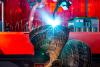
Additive Manufacturing Design Contest for Young Engineers 2021 - Apply now!
During the annual conference Meeting Materials, organized by M2i, the Grade2XL project will organize an open Additive Manufacturing Design Contest for young engineers as part of the Grade2XL project.
GOT WHAT IT TAKES?
-
Are you enrolled in a Bachelor, Master or PhD degree program at a European university? Or are you a young professional who is still under the age of 35 years on 14 December 2021?
-
Do you have an idea for a 3D printed component that can be made with the wire arc additive manufacturing technology?
-
Are you passionate about technology and want to see your ideas take shape?
GRADE2XL
The Design Contest is part of the Horizon 2020 project Grade2XL. This project will demonstrate the potential of multi-material wire arc additive manufacturing (WAAM) for large structures. Grade2XL will deliver multi-material products of superior quality and performance, cut lead times by up to 96% and enable massive savings for the maritime, energy and industrial machinery sectors. The Grade2XL consortium is led by M2i and gathers 21 partners from eight European countries, top innovators in the field of wire arc additive manufacturing.
CRITERIA
The following criteria will shape the selection process:
-
Novelty: new geometry, impossible to manufacture with conventional processes;
-
Functionally graded: showing added value of multi-material composition, i.e. different properties at different locations;
-
Purpose: the design should be intended for a real engineering application.
SCORING CRITERIA
There is a maximum score of 10 points:
-
Novelty: The extent to which the proposed design is a new geometry impossible to manufacture with conventional processes. Score 0-3
-
Functionally graded: The extent to which the proposed gains (material or financial savings) when a multi-material approach is used, i.e. different properties at different locations. Score 0-3
-
Purpose: The extent to which the design is suitable for an existing engineering application. Score 0-3
-
Bonus point: Potential to impact the industry i.e. transferability of the approach towards other applications and sectors. Score 1
JURY
The Jury consist of five experts working in the field of WAAM, in academic and industrial organisations which are at the forefront of WAAM.
THE PRIZE
One winner/winning team will have their part manufactured at RAMLAB in Rotterdam. If the designed part is heavier than 20 kg, a representative component of up to 20 kg will be printed. The winner/winning team will be selected via a blind procedure.
DEADLINE
The submission deadline is 19 November 2021. The winner will be announced during the M2i "Meeting Materials" Conference on 14 December 2021.
APPLICATION
Make sure you download one of the application forms on the Grade2XL website available here. In the form you will find all information necessary for submitting your design.
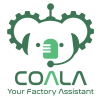
COALA Newsletter #1 - Vision and Human-AI Collaboration in Quality Control of White Goods
|
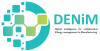
Pathways to Energy Efficient Manufacturing workshop at Sustainable Places 2021
On the 28th of September, the DENiM team will lead a virtual cross project collaboration involving four H2020 projects funded under the FoF-09-2020 programme (DENiM, EnerMan, Ecofact & ECO2MATION) as part of the sustainable places conference taking place between 28th Sept – Oct 1st in Rome (Physical & Virtually)
The virtual workshop will take place on the 28th Sept 15:30 CET, please attend to join the community and share your views and experience through interactive sessions to help industry define clear pathways to achieve energy efficient manufacturing.
The workshop is free but registration is required, here is the invitation link, this will require you to create a profile on the conference platform (how to article here)
AGENDA
- Introduction
- Project Overview & Challenge Perspective
- DENiM
- ENERMAN
- ECOFACT
- E2COMATION
- Interactive/Virtual White Boarding session
- Review/capture synergies across projects (Miro activity)
- Round table discussion on barriers, challenges and opportunities covering (Miro activity)
- Pathway Setting: Rank opportunities/next steps as to where industry needs to go to continue to address the energy efficiency (Miro activity)
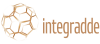
Digital Thread for Additive Manufacturing: Integradde´s video is out now!
This video shows how the Integradde´s Digital Thread for Additive Manufacturing works step by step and how it has been validated in 4 Pilot Lines across Europe in real manufacturing conditions!
> Watch the Integradde´s video here!
Would you like to implement Additive Manufacturing in your production processes at no cost? Apply to Integradde´s Expression of Interest!
European SMEs and MidCaps willing to implement Additive Manufacturing in their production processes are called to participate in the Integradde´s Expression of Interest (EOI). The selected winners will access the expertise and services (valued in 20K/service) provided by Integradde´s Open Pilot Network AT NO COST!
Make sure to submit your application before September 30th: https://expression-of-interest-integradde.fundingbox.com/
Learn how to build a winning application: Join us on September 8th at 11:00 for the Integradde´s EOI Infoday!
We have some tips for you to help you build a winning application! Join us at the Integradde´s EOI Infoday that will take place on September 8th at 11:00 CEST where we will address some frequently asked questions about the process and useful guidelines to make an outstanding application also, if you have some other questions or doubts this is the time for you to take the stage and get answers!
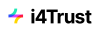
The first Open Call for i4Trust is now open!
i4Trust launched the first of two open calls to select up to 16 Bottom-up Experiments that seek to implement experiments that demonstrate how already existing processes can be improved or new innovative services can be created by means of sharing data among multiple companies using i4Trust.
Deadline for submission: 6th September 2021 (14:00, CEST).
APPLY NOW!
We are looking for consortia composed of SMEs/slightly bigger companies (minimum 3) and 1 DIH registered in any of the following countries:
- the Member States of the European Union and its Overseas Countries and Territories (OCT) or
- Associated Countries to H2020
- The United Kingdom
Selected beneficiaries will become part of a customized 9-month i4Trust Data Sharing Mentoring Program, which includes:
- Refinement of the proposed Use-Case definition
- Mentoring support for workforce re/up-skilling
- Mentoring support on legal, operational, technical and business matters
- Support on i4Trust technologies (building blocks)
- Funding as a lump sum, ranging from €72,000 to €120,000 per consortium
Visit our website to find more info i4Trust Open Call site and join i4Trust community
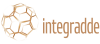
Integradde´s Expression of Interest is open as from today (June 1st)
The INTEGRADDE project launched today (June 1st) an Expression of Interest (EOI) Call, oriented to European SMEs and Midcaps willing to implement Advanced Manufacturing solutions in their production process.
The call will be open from June 1st until September 30th and will select 5 companies to receive selected services (such as Free-Trials) from the ‘Network of Open Pilots Lines’ Catalogue of Services.
The Expression of Interest will choose 5 beneficiaries which will receive services from the ‘Network of Open Pilots Lines’ catalogue of services. The open pilot line network is made of four RTOs, each of them providing different schemes and AM processes:
- AIMEN Technology Centre: owning different robot-based cells for LMD-powder (LMD-p).
- WEST: owning different robot-based cells for WAAM and LMD-wire (LMD-w).
- CEA: provides access to robot-based workstation for WAAM and different equipment for inspection of AM components.
- IREPA: owning CNC-based cells for LMD-p and robot-based LMD-w with capability to process Titanium.
One additional beneficiary will receive these services from MX3D, the innovation leader in 3D metal printing and partner of INTEGRADDE.
The entire application process is carried out through the open call management site hosted at Fundingbox, while the information about the EOI is published in the Integradde community (make sure to join!)
Check the Guide For Applicants for information on the requirements for participation and the detailed free services the winners will get in the link below and APPLY NOW!
GET ALL THE INFORMATION AND START YOUR APPLICATION HERE!
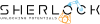
“ROS drivers suite” for COMAU robots
ROS, which stands for Robotic Operating System, is an open-source robotics middleware. Nowadays, it is increasingly being used in research as well as industrial applications due to the flexibility it offers. ROS provides peer-to-peer communication among various devices, is lightweight and supports multiple programming languages.
SHERLOCK consists of 19 hardware and software modules. Following a versatile approach, communication among the modules is being achieved via ROS, either using existing ROS interfaces or building them from scratch.
In this context, LMS developed the necessary drivers that provide ROS support for the COMAU AURA and Racer5L cobots, enabling their communication with the rest of the SHERLOCK ecosystem.
The developed “ROS drivers suite” offers the following main features:
- Asynchronous robot control
- I/O control
- Fieldbus control
- Synchronous robot control (sensor tracking)
Asynchronous robot control: The robot publishes its state to the ROS driver with a frequency of 100Hz. During this operation, two ROS action servers are responsible for moving the robot, one for joint space trajectories and one for cartesian space trajectories. The desired trajectory is sent from the ROS application (e.g., MoveIt) as a goal for the robot. Functionalities such as validation that the goal is inside the robot limits and that it is ready to receive a new goal are also implemented.
I/O control: This part of the “ROS drivers suite” is responsible to enable/disable the hard-wired I/Os of the robot. A dedicated ROS service offers control over the physical of virtual GPIO pins of the controller while providing feedback regarding their state.
Fieldbus control: This part of the “ROS drivers suite” is responsible to control devices connected to the robot controller via Fieldbus (PROFINET, PROFIBUS, Ethernet IP), as well as monitor their state.
Synchronous robot control (sensor tracking): The difference of the synchronous robot control compared to the asynchronous one is that in the synchronous control, the robot is correcting its trajectory in real-time based on feedback received from dedicated sensors (force/torque sensors, vision systems etc.) The control loop frequency can be as high as 500 Hz, ensuring quick and smooth corrections. The user (ROS application) can move from asynchronous to synchronous robot control mode at any time.
“ROS drivers suite” includes two more applications. The “COMAU robot simulator” which allows the user to perform a simulation for a given application without the need of a physical robot, and the “MoveIt interface” which enables the on-the-fly trajectory planning (either in physical or virtual application).
It is worth noting that, apart from the AURA and the Racer5L robots, this “ROS drivers suite” supports a variety of COMAU robots that use the C5G controller, such as NJ4 110-2.2, NJ4 170-2.9, NJ 220-2.7, Racer 5-0.80, Racer 7-1.4.
For more information, you may visit the website of the project.
Photos --> link 1
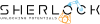
COMAU Racer5 Cobot released to the market!
SHERLOCK is pleased to announce the first, early, commercially exploitable result of the project, COMAU Racer5 Cobot, a new paradigm in collaborative robotics, designed and commercialized by COMAU.
COMAU, a well-known Italian robotics manufacturer and industrial partner of SHERLOCK, just released to the market their newly developed low-payload collaborative robot.
Driven by the requirements of the industrial use cases of SHERLOCK, aligned with the market needs, COMAU developed within the project a low payload collaborative robot with payload of 5Kg.
It is currently the only collaborative robot able to automatically switch from industrial robot speed to collaborative speed. This feature allows it to work in full -industrial- speed when the operator is far away from the robot while reducing its speed to lower -collaborative- speed when the operator enters its working area. Thus, increased flexibility and productivity, as well as reduction of cycle time, can be achieved.
Moreover, Racer5 cobot offers an intuitive, non-intrusive programming framework. The operator is able to effortlessly move the end effector and teach robot motion using hand guidance.
Racer5 cobot is a certified product, complying with all the safety derivatives relevant with human-robot collaboration.
For more information, you may visit our website.
Publication “RECLAIM: Toward a New Era of Refurbishment and Remanufacturing of Industrial Equipment”
RECLAIM presents a new idea on refurbishment and remanufacturing based on big data analytics, machine learning, predictive analytics, and optimisation models using deep learning techniques and digital twin models with the aim of enabling the stakeholders to make informed decisions about whether to remanufacture, upgrade, or repair heavy machinery that is toward its end-of-life.
This publication in the Frontiers in Artificial Intelligence shows how the integration of RECLAIM technological solutions into industrial environments can lead to industries having an extra economic income from the extended lifetime of manufacturing systems and their components, which can be achieved by adopting refurbishment and remanufacturing solutions.
Get more details about the content and download the paper in our project website here!
UPTIME Newsletter - March 2021 edition
Welcome to the 8th edition of the UPTIME Newsletter.
The UPTIME project has officially ended in February 2021. After 3,5 years of research and development, the UPTIME Platform is ready now for the market. The UPTIME consortium has defined a concrete go-to-market strategy to optimize the impact of the UPTIME Platform on the market and maximize its chances of success. The consortium feels this is the right time to launch a new solution for predictive maintenance with all of the advanced features the UPTIME Platform and its substituent components offer.
UPTIME proposes a differentiating value proposition, and its business model offers enough flexibility to reach a wide range of companies of different size and type. The market-oriented website – www.uptime-predictive-maintenance.com – with clear key messages and its demo-space is a good tool to get new leads and will be further built upon and utilized going forward in the exploitation activities. An adoption methodology for UPTIME deployment has been also created according to the successful deployment in the three business cases and is introduced in this Newsletter.
The consortium plans to drive forward the convergence of the UPTIME Platform with Industry 4.0 standards and beyond that, to address the issues that are beginning to be championed under the banner of Industry 5.0.
A strong foundation has been laid for the convergence with Industry 4.0 in the full compliance of the UPTIME Platform with the RAMI 4.0 reference architecture and addressing Asset Administration Shell (AAS) interoperability. The next step is to realise the AAS interface more fully and establish the UPTIME Platform as a Digital Twin for asset maintenance.
Events such as the 2nd UPTIME showcase event will be repeated since they proved extremely helpful in overcoming constraints imposed by the COVID-19 pandemic, however a live and in-person event will be organized as soon as possible in the post-project commercial phase. As a first step, UPTIME will be hosted by BIBA at Digital Hannover Messe event, which will take place from 12 – 16 April 2021. We’d like to take this opportunity to invite you to join us virtually at this event. You can register your participation free of charge using the ticket code “CVJVm” through this link.
On a wider scale, the cooperation begun in the framework of the ForeSee cluster will also be maintained by the UPTIME partners, to contribute in the implementation of its structured Predictive Maintenance roadmap and to have a greater impact on standards and production of commons for European industry, which will shape the access to the new market of maintenance, which is key for the industry of the future.
A full newsletter is available: https://www.uptime-h2020.eu/index.php/2021/03/31/uptime-8th-newsletter-edition-03-2021/
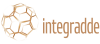
Registration is now open for INTEGRADDE Online trainings!
Join the INTEGRADDE training sessions: Additive Manufacturing for Manufacturers and Final Users
The INTEGRADDE consortia has come together to offer you a 2-part online training session on June 25th and July 2nd on Additive Manufacturing.
This is an optimal way of transferring the knowledge and know-how obtained through the development of the project activities to the entire sector, including academia, professionals and public authorities.
The main objectives of these trainings are, on one hand, present the benefits for the industry of the technologies developed within project and, on the other hand, boost the acceptance and integration of the project results in the Advanced Manufacturing value chain.
This is a one-of-a-kind opportunity for entities and professionals in the sector to get first-hand information on how to apply these technologies, gain confidence about their use and stay at the forefront of the industry´s future.
On the agenda:
The first session will take place on June 25th and will be oriented to manufacturers. The main topics covered will be:
- Design for Additive Manufacturing
- Material procurement
- Process with focus on WAAM and Laser
- Post processing
The second session will take place on July 2nd and will be oriented to final users. The main topics covered will be:
- General introduction to Additive Manufacturing
- Market of Additive Manufacturing and expectations
- Modelling
- HSE (Health, safety and environmental protection in the manufacturing sector)
- Standardization
- Quality and Certification
Both sessions, organised by Bureau Veritas, will be taught by experts from top-level organisations and companies, among them:
- ESI Group
- MX3D
- German Institute for Standardization (DIN)
- AIMEN Technology Centre
- Bureau Veritas Group
- Laboratory for Manufacturing Systems & Automation at University of Patras
Do not miss this opportuniy and BOOK YOUR TICKET here!
Join the INTEGRADDE community for more events and opportunities in Advanced Manufacturing.
Call for Papers (ETFA 2021): Refurbishment and re-manufacturing of machinery in CPPSs
The RECLAIM special session at ETFA, the 26th International Conference on Emerging Technologies and Factory Automation (7-10 September 2021 in Sweden) provides researchers and practitioners from the industry with a platform to report on recent advances and developments as technological enablers supporting value retention throughout the industrial equipment lifecycle.
Call for proposals | Submit your paper
- Submission deadline: (regular papers) extended to 7 May! | (Work-in-progress/Industry practice papers) 13 May
- Acceptance notification: June 10
- Deadline for final manuscripts: June 17
Topics include (but not limited to):
- Big data analytics, predictive analytics, and optimisation models using deep learning techniques, and digital twin models.
- Models for informed decision about whether refurbish, remanufacture, upgrade, or repair machinery that is towards its end-of-life.
- Technologies and strategies to support a new paradigm for refurbishment and remanufacturing of industrial equipment in factories.
- New concepts and strategies for repair and equipment upgrade and factory layouts’ redesign.
- Optimal refurbishment and re-manufacturing of electromechanical machines and robotics systems.
- IoT sensors, novel prediction, and process optimisation techniques to offer machine lifetime extension.
- Innovative fog computing and augmented reality techniques combined with enhanced health monitoring and failure inspection and diagnosis.
- Approaches for the servicing and upgrading of legacy equipment evaluation and demonstration of approaches in real industrial environments.
More info: Refurbishment and re-manufacturing of machinery in Cyber-Physical Production Systems
About the EU project RECLAIM (H2020): RE-manufaCturing and Refurbishment LArge Industrial equipment: Manufacturing is a pillar of innovation and growth for Europe, but outdated machinery and unplanned downtime can cause significant losses for companies and employees. RECLAIM provides techniques, strategies, and decision-making tools to reduce machine obsolescence, improve predictive maintenance and upgrade legacy machines. The project partners will demonstrate the advantages of high-tech refurbishment and reuse of large production equipment and lines in 5 industrial sites across sectors – welding, woodwork, textiles, robotics/white goods and footwear, and initiate replication in further sectors. Don't hesitate to get in touch!
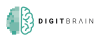
Digital twins for manufacturing: EU innovation Project DIGITbrain will give SMEs easy access to digital twins through Open Call
DIGITbrain Project, which is funded by the EU Research and Innovation Programme Horizon 2020, aims to enable small and medium-sized European manufacturing companies (SMEs & mid-caps) to benefit from AI-based Manufacturing-as-a-Service (MaaS). In its first Open Call from March 2021 to June 2021 the project will accept new applicants and support the implementation of seven industrial use cases in the field of manufacturing with up to 100K Euros.
DIGITbrain in a nutshell
The Digital Brain is a completely novel concept that extends the Digital Twin to cover the full lifecycle of industrial products and thereby expands it to a smart entity having analysis and decision support capabilities. By having access to on-demand data, models, algorithms, and resources for industrial products the "Digital Product Brain" will, enable their customisation and adaptation according to very individual conditions and thus, facilitate the implementation of Manufacturing as a Service for SMEs. This will not only accelerate adaptation of manufacturing and products to changing conditions, and enable personalized manufacturing in an affordable way, but also facilitate cost-effective distributed and localised production, allowing them to access advanced manufacturing facilities within their regions or to distribute their orders across different ones.
Apply for the project until the end of June 2021 with your industrial use case and join a Pan-European Team that helps solving it!
In its lifetime the project will implement 21 highly innovative experiments, each bringing together suitable manufacturing end-users, technology providers, research organisations, High Performance Computing providers or Digital Innovation Hubs, in order to implement an individual use case-based Digital Twin.
Who can apply?
Companies from the above mentioned groups, located in the EU, a Horizon 2020 associated country or the UK, can apply in one of the two Open Calls, with their specific use case. Experiments can cover all segments of the entire manufacturing sector, e.g. discrete manufacturing, continuous production or construction. In its first Open Call, open from 31st March 2021 to 30th June 2021, it will add 7 new experiments, eligible by up to 100K Euros each. The experiments will be integrated to a Digital Marketplace, which provides the necessary graphical user interfaces (GUIs) in view of configuring and monitoring the Digital Brain for an industrial-product instance and will handle the access rights to the Digital Brain’s instances.
The Project is funded by the EU Research and Innovation Programme Horizon 2020 under grant agreement number 952071 and currently composed of a consortium of 36 partners.
DIGITbrain Open Call Details:
- DIGITbrain will be running 2 Open Calls for experiments all over Europe with a budget of: 1 400 000 € which you can apply to
- 1st Open Call: From March 2021 to June 2021
- 2nd Open Call: From March 2022 to June 2022
- 7 application experiments will be accepted in every Open Call and receive
- up to 100K Euros per experiment
- up to 60K Euros (possible) per third party
DIGITbrain Open Call timeline
- Opening date: March 31st, 2021 - 10:00h (CEST Time)
- Proposal submission deadline: June 30th, 2021 - 17:00h (CEST Time)
- Proposal evaluation phase: from June 30th to the end of September 2021
- Announcement of accepted proposals: September 2021
- Support throughout the process (application, design and implementation of the experiment) by the participating Digital Innovation Hubs.
- Begin of implementation phase: October 2021
ECSEL Industry4.E Lighthouse | Bringing Projects Together | Workshop
Today we bring together an exclusive group of experienced research and innovation project partners to get first-hand insight into the key exploitable results from projects including ECSEL Industry4.E and Horizon 2020 as we prepare for the Horizon Europe, Cluster 4, Digital Industry and Space, September call deadlines and future R&I collaboration opportunities together.
Time: 1200 – 1400 CET
Date: Thursday 11th of March 2021
Location: Microsoft Teams
The presentation and recording will be available here shorlty for further innovation and collaboration opportunities.
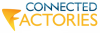
ConnectedFactories Cybersecurity Workshop - presentation and recordings are available
The ConnectedFactories Cybersecurity workshop took place on the 20 January 2020. Presentation and recordings are available here: https://www.connectedfactories.eu/events/cybersecurity-workshoppresentations-and-recordings
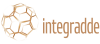
An Open Pilot Line at IREPA LASER
IREPA LASER is an industrial research and development company specialized in laser processes and materials, with a laser machine base including over 20 devices to support all companies in their needs.
The main service is to offer customers tailored industrial solutions to support them in their product development and manufacturing engineering projects. This service is focused on three main skill areas: Additive Manufacturing, surface functionalization and welding. IREPA LASER is also a laser training centre and can train individuals in the use of laser technology.
IREPA LASER is involved within INTEGRADDE project for the development of a new manufacturing methodology capable of ensuring the manufacturability, reliability and quality of a target metal component from initial product design via Direct Energy Deposition (DED) technologies. An open-pilot line will be implemented at IREPA LASER, which will allow a continuous validation and deployment of specific developments towards industrialization.
The general INTEGRADDE concept and end-to-end the solution is being deployed at IREPA facilities to test and review as early adopter of this manufacturing methodology. Data collected from different steps are implemented through the digital thread with the final aim to improve the quality of the parts manufactured.
The development of this concept uses of the equipment features of IREPA LASER.
A machine is dedicated to DED-powder (MAGIC system) with 2 lasers (IPG YLR500, and IPG DLR2000), the original MacroCLAD head from IREPA LASER, and a powder feeder from MEDICOAT.
A new hardware has been recently implemented at IREPA LASER. This new robotic system consists of 2 robots, one of which is installed on a linear 5m axis, a rotary table able to support 3T. 2 fibre lasers (IPG laser YLS) bring their laser beam to the DED-powder and DED-wire heads. Profinet network is used to connect and control all this equipment. This novel machine has been designed in order to work on a large scale parts (up to 5m long), with the selected two processes: DED-powder and DED-wire.
Using previous existing LMD-p infrastructure, several developments on process window development, monitoring and control have been carried out. Particularly, efforts have been focused on data collection from CNC and image-based process monitoring information. Data are collected from process sensors (such as image-based data from an NIT camera, temperature) and CNC positions synchronously during the additive manufacturing process. These datasets have been processed, in collaboration with AIMEN, NIT, ATOS and CEA, to generate a 3D representation of the parts being built.
Concerning the digital thread, IREPA has recently migrated on a new CAD-CAM software: SIEMENS NX with the ‘multiaxis deposition module’ for DED machine programming. In collaboration with the partner ‘University of Coimbra’, the use of the AML format in development.
Process development is carried out by using the two DED processes: DED-p and DED-w.
Concerning the DED-w, the PRECITEC Head named ‘Coax Printer’ is used. The upgraded version of this head has been recently received and implemented. It allows recording the interaction between beam-wire-substrate during the deposition with a coaxial vision in order to get more data for the control process.
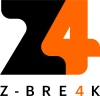
ForeSee WEBINAR - Application of #Standards by factories of the future for Predictive Maintenance
ForeSee WEBINAR - Application of Standards by factories of the future for Predictive Maintenance
When? January 28th from 4.30 pm CET
Topic: Best practices for standardisation activities and improvements for industrial IoT and smart manufacturing
Registration link: https://bit.ly/3c7yywY
Further information at this link: http://foresee-cluster.eu/
UPTIME Newsletter - November 2020 edition
Welcome to the 7th edition of the UPTIME Newsletter.
The UPTIME project has entered the final phase. The prototype of the UPTIME Platform has been deployed into the three industrial business cases in its final configuration.
The UPTIME Platform gives you a competitive advantage by empowering everyone involved in your maintenance activities. Operational staff and managers benefit from real-time visualization of asset conditions, correlation analyses and accurate predictions. Maintenance managers benefit from actionable plans based on accurate predictions, increasing efficiency and reducing costs. All stakeholders gain valuable insights into the data thanks to intuitive, customizable visualization. In this edition, we gladly present you 10 main added-values of UPTIME Platform perceived by our industrial end-users.
In addition to the six main components of the UPTIME Platform introduced in the previous newsletters, in this issue, we are proud to announce the UPTIME Workers’ Mobile Application, which helps workers on the shop floor stay up-to-date in real-time about their maintenance tasks.
A full newsletter is available: https://www.uptime-h2020.eu/index.php/2020/11/20/uptime-7th-newsletter-edition-11-2020/
UPTIME 3rd Live Webinar: Predictive Maintenance: Lessons Learned and Best Practices in Aviation Industry - 10 Dec 2020
Date: Thu, 10 December 2020
Time: 11:00 - 12:30 CET
The UPTIME 3rd Webinar will address benefits of predictive maintenance in a highly complex transportation asset operations deployed in the aviation industry. UPTIME Partner from FFT Produktionssyteme GmbH & Co. KG will share his experiences, challenges and some lessons learnt from the implementation of the UPTIME Platform in the FFT use case.
The use case focusses on one specific production logistics asset used in the aviation industry, so-called “jig” for the transport of wing covers of commercial aircraft. The reliability of production logistics assets is a critical cost factor in the production of high-value products such as aircraft and needs to be considered along with the reliability of other production equipment to ensure a timely, cost-effective and high-quality production processes. Due to the critical nature of the deployment of these assets, the requirements are both technically and organisationally very high. The need has arisen to increase efficiency in maintenance execution as well as in reporting to the client, who in most of our projects is responsible for the logistics coordination of their assets.
The web seminar is free of charge, dedicated to people who want to learn and see a concrete implementation of the UPTIME Predictive Maintenance Platform in a real business case. It is interactive, where you have the opportunity to ask questions to the experts panel and we are happy to receive your feedback.
If you have any questions or comments, please contact us.
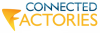
Registration is now open - Cybersecurity workshop: 20 January 2020
We kindly invite you to register for the Cybersecurity workshop on the 20 January 2020 organised by ConnectedFactories 2.
Register here and download the agenda
The online workshop will provide an insight into the recent developments of projects that focus on cybersecurity in manufacturing: SeCoIIA and COLLABS project.
It will also provide an insight into how cybersecurity aspects are addressed in other projects that focus on the digitalisation of manufacturing and the deployment of digital platforms (see https://www.connectedfactories.eu/origin-project-and-outreach ).
Have a look also at the presentation on CyberSecurity Related Standards by Ulrich Seldeslachts, LSEC (recording & presentation) from the recent ConnectedFactories Webinar on Standards for digital manufacturing.
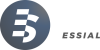
ESSIAL video pitch at the Rev3 Energy Day
ESSIAL has been selected to participate in the Rev3 Energy Day (2 December 2020, online) with a video pitch presenting the project followed by a round table with the coordinator.
The Rev3 Energy Day will take place on 2 December 2020, from 16:00 to 19:00 online. This annual event, organised by the Energy Pole and the MEDEE Cluster, aims at bringing together research and industry. Its objective is to raise compagnies' awareness of the energy research work carried out in the Hauts-de-France Region (Northern France) and to encourage the emergence of new collaborative projects.
In this context, ESSIAL has been selected to present the project through a 4-minute video pitch. The video (online soon) highlights the technical, economic and environmental impact of the project, as well as its applications. The pitch will be followed by a round table discussion with ESSIAL coordinator Olivier Maloberti (ESIEE Amiens).
Free registration here.
The event will be held in French.
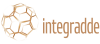
Standardization in INTEGRADDE
In research projects, especially when public funding is provided, the effective, economic usability of the results is increasingly in the focus. Research projects must therefore be holistically and long-term oriented. For this purpose, DIN offers many years of expertise to provide optimum support for the market transfer and dissemination of innovative results from research and development.
In INTEGRADDE, DIN is the partner for questions concerning standardization. DIN coordinates the standardization activities of the project. These activities comprise the knowledge transfer regarding standardization, the development of an overview of the current standardization landscape in the subject area AM as well as the development of accompanying standardization measures.
To foster the knowledge transfer a special standardization training was developed aiming to enable the project partners to develop and pursue joint standardization activities.
The overview of the current standardization landscape provides a detailed research on relevant standardization committees and corresponding standards.
In the case of INTEGRADDE, it quickly became clear that ISO/TC 261 "Additive Manufacturing" is trend-setting in AM and that close cooperation should be targeted.
Due to the very different knowledge base in INTEGRADDE about standardization DIN has developed a standardization training especially for the INTEGRADDE project. The aim of the training was to provide knowledge enabling the project partners to develop and pursue joint standardization activities. Furthermore, the training emphasizes the high relevance of standardization for AM and is meant to motivate the project partners to follow current developments in standardization committees as well as to document and disseminate the knowledge acquired in INTEGRADDE in the long term. The training is divided into the following five chapters: Meaning, structure, integration, AM, follow-up. Each chapter has its own conclusion with the most important information in order to realize an easy understanding and the highest possible absorption of the knowledge.
The training provides information on why it is important to push the issue of standardization both from the beginning and continuously and what the benefits of standardization are. This is followed by an explanation of the basic principles of the working method and the underlying process. The third chapter presents the possibilities for participation and gives an assessment of the resources required for participation.
In the chapter specifically focusing on AM, the most important standards are listed and the standards research carried out is explained. In addition, the structure of the standardization committees in the area of AM is explained before finally reaching a conclusion with the most essential information.
After these cornerstones were laid, the actual standardization started. Challenges faced by the project partners due to gaps in standardization were assessed with the help of a two day workshop. On day one the project partners were asked to position themselves within the INTEGRADDE process as well as to identify and to prioritize current challenges with regard to standardization. On the second day of the workshop the challenges were compared to current and planned standardization projects of ISO/TC 261. These comparisons have been discussed and it was determined in which projects INTEGRADDE should participate or comment. The following key issues of INTEGRADDE for standardization could be identified:
· Digital thread
· Quality assessment (operator, machines, process)
· Software interoperability
· Process safety
· Testing (software, non-destructive, destructive)
· Properties(feedstock conditions, material, finished parts (e.g. defects))
· Design methods
· Terminology
Based on these results a common standardization strategy for the INTEGRADDE project has been prepared. Especially the standardization idea of the "digital thread" for which there is currently no current or planned standardization project is of great importance for the INTEGRADDE project. For this reason, the project is currently striving for close cooperation with ISO/TC 261/WG 4 "Data and Design". With the development of the standardization strategy, an important milestone was accomplished regarding standardization. The further implementation of this strategy will be coordinated and supported by DIN.
As steps in standardization DIN will continue to pursue a close collaboration between the standardization bodies and INTEGRADDE. One step will be to contribute to the assessed standardization projects. DIN further will identify the responsible groups within ISO/TC 261 for the remaining standardization ideas and check how these can be addressed best.
http://www.integraddeproject.eu/590/standardization_in_integradde
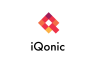
1st iQonic funded paper published by Brunel University London
We are happy to announce our first iQonic funded paper published by Brunel University London. The publication is a comprehensive review article that highlights the importance of automatic optical inspection in electronics industry.
The article is available in the following link.
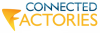
Digitalization of Manufacturing: Building the ecosystem for a smart and sustainable future
The Digitalization of Manufacturing: Building the ecosystem for a smart and sustainable future event is on the 12sd of November 2020, within the framework of the 2020 edition of the World Manufacturing Forum. It is co-organized by Smart Anything Everywhere, Politecnico di Milano, MADE Competence Center and DIH Lombardia.
This event will bring together European, national and regional initiatives aimed at boosting the digital transformation of manufacturing, to share available opportunities and good practices, and discuss about synergies to work together.
The audience will find out about technologies, funding and collaboration opportunities offered by the “Smart Anything Everywhere” European Initiative to foster the digitalization of SMEs and midcaps. Moreover, the audience will have the opportunity to get lessons learnt and recommendations about the on-going development of the European Digital Innovation Hubs Network building bridges between the European and the local level.
Register here and join the event live to interact with the speakers.
Find the full programme - here
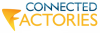
Presentations and recordings available - 'Standards for Digital Manufacturing Webinar' - 20 October 2020
The presentations and recording are available here.
You are also invited to follow the ConnectedFactories2 project and other projects of your interest via the EFFRA Innovation Portal’s weekly digest functionality , you can find out more information on how to do this here: https://www.connectedfactories.eu/follow-connectedfactories-effra-innovation-portal-weekly-digest

Join the iPRODUCE event | The Social Manufacturing Paradigm: co-creating with manufacturers, makerspaces and consumers
:: REGISTER NOW! ::
In recent years, every day citizens have had an increasing amount of opportunities to actively participate, contribute and decide in different areas and contexts. Although these opportunities are still emerging, the manufacturing industry is no exception to this paradigm.
The objective of the online event – The Social Manufacturing Paradigm: co-creating with manufacturers, makerspaces and consumers – is to highlight the role of makers and consumers in the social manufacturing landscape, which promotes the participation among individuals and the industry in the production of consumer goods.
This framework will be made based on the activities being carried out within the iPRODUCE project. The presentations will focus on highlighting the main requirements and challenges faced by consumers and the industry and technologies that are available to facilitate a collaborative manufacturing environment. Invited speakers will showcase ongoing work and existing practices within the domain of social manufacturing. Finally, a virtual round table will provide the audience with an opportunity to engage and manufacture a fruitful and interactive discussion.
Preliminary agenda:
09h30 | Virtual hello and welcome
09h45 | Introduction of iPRODUCE
10h00 | The social manufacturing paradigm: needs, practices and tools
10h30 | Keynote 01
11h00 | Break
11h15 | Keynote 02
11h45 | Presentations from iPRODUCE collaborations
12h15 | Virtual round table
12h45 | Wrap up and end of event
More information on the iPRODUCE website:
:: REGISTER NOW! ::
Industry4.E Lighthouse Newsletter - August
See the Industry4.E Lighthouse newsletter here https://mailchi.mp/1ed66f7454cd/industry4e-e-newsletter-issue-one
Please subscribe to receive future newsletters directly
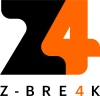
Predictive Maintenance: European success stories - 1st ForeSee webinar
On September 24th join the #ForeSee cluster for the 1st #webinar on"Predictive Maintenance: European success stories"!
We'll talk about Platforms and Microservices for manufacturing operations with Prof Sotiris Makris & Kosmas Alexopoulos from the University of Patras and we’ll present @WhirlpoolCorp & @IDEKO demonstrations!
Register for participating: https://www.crit-research.it/en/eventi/predictive-maintenance-webinar-series-european-success-stories/ https://www.crit-research.it/en/eventi/predictive-maintenance-webinar-series-european-success-stories/
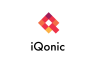
TOWARDS THE DEVELOPMENT OF THE IQONIC ARCHITECTURE FOR ZERO-DEFECT MANUFACTURING OF OPTOELECTRONIC COMPONENTS
The 1st phase (M1-M18) of the iQonic project has just concluded with the 1st Review Meeting with the Project Officer and Monitor. After the collection of requirements, the identification of optoelectronic functionalities and the development of the HW and SW solutions that will compose the iQonic architecture for the zero-defect manufacturing of opto-electronic components, the main technologies and methodologies are now ready for the testing, validation and integration in relevant use-case scenarios.
In the first phase of the iQonic R&D activities, the needs and expectation of the consortium as well as of project’s stakeholders were closely observed and extracted from the project use-cases – ALPES LASER, PRIMA ELECTRO, FILAR OPTOMATERIALS and BRIGHTERWAVE. These results have been collected in a detailed list of technical and non-technical requirements and specifications. Moreover, optoelectronic functionalities for each use case, the generic development frameworks for the assembly processes and the data input and output points in the process chain were defined.
This enabled the development and laboratory testing of the iQonic HW and SW technologies, including the iQonic sensorial network, adaptive optics and electronic nose for evaluation of materials, smart grasping robotic for flexible handling and the Knowledge Based System. In parallel with technical development, a set of innovation management activities took place aiming to develop the roadmap to introduce the iQonic technology to the market, after the end of the project.
In the next months, these technologies will be integrated in the iQonic optoelectronics manufacturing architecture and together with the definition of defect detection and classification techniques – 3D imaging methodologies and smart tagging, defect severity evaluation and decision support systems (DSS), processes and tools for reuse or requalification – and defect management techniques – Predictive Maintenance functionalities: Cyber Physical System – CPS, end-of-life management, Reverse Supply Chain – will pave the way towards zero-defect manufacturing of opto-electronics and photonics.
Eventually, starting from the project 2nd phase (M19-M30), iQonic solutions will be integrated and validated at the shop floor level in several demonstrators at iQonic end-users’ facilities. The full version of the press release can be found in iQonic website.
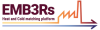
Link to project news here
Please find all news on the project at https://www.emb3rs.eu/news/
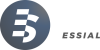
ESSIAL Virtual Technical Workshop - Andaltec
ESSIAL International Technical Workshop will take place online on 10 September 2020. This event is organised by ESSIAL's partner Andaltec (Centro Tecnológico del Plástico). This event was initially planned on 26 March 2020 at Andaltec Heaquarters in Martos (Jaén), Spain, but had to be cancelled due to the COVID-19 outbreak. Finally, the workshop will be organised virtually as a webinar.
The workshop aims at presenting the project results and engage the stakeholders into personal interactions with the project participants. It is open to researchers, engineers and SMEs that may be interested in such a new technology.
Below, the programme of the workshop:
- 10:00: Opening - José María Navarro, General Manager at Andaltec
- 10:15: ESSIAL project presentation and laser welding process - Jesús Castillo, R&D engineer at Andaltec
- 10:30: Electrical steel manufacturing process and microscopy analysis in ESSIAL project - Jean-Pierre Birat and Camille Pineau, consultants and researchers at IRT-M2P
- 11:15: Break
- 11:45: ln-line monitoring techniques and upscaling strategies to optimize the manufacturing time and costs - Anne Henrottin, R&D Engineer at Lasea
- 12:30: Impact of local surface laser treatment on magnetic properties of grain-oriented silicon iron sheets - Manar Nesser, PhD student at UPJV in collaboration with ESIEE-Amiens
- 13:15: End of the Webinar
Registration:
Registration is free of charge. You are just required to send your contact data (company name. number of attendants and e-mail address) to jesus.castillo@andaltec.org. The participants will receive the information to access the Webinar platform upon registration.
More information on the ESSIAL Website!
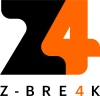
ForeSee Cluster Webinar Series
Predictive Maintenance: European success stories
The ForeSee Cluster has launched a series of webinars to discuss about the breakthrough Predictive Maintenance innovations achieved by its members.
Have a look at the program and subscribe to the 1st meeting to know more on our PdM solutions!
Program: http://foresee-cluster.eu/wp-content/uploads/2020/08/ForeSeeWebinarSeries.pdf
For further information on the initiative: https://www.z-bre4k.eu/news/foresee-cluster-webinar-series/
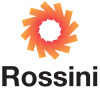
Rossini’s recent advances in the cognitive layer for collaborative robot control - Press release
Please, find at this link the most recent updates on the Rossini project: https://www.rossini-project.com/news-and-events
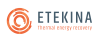
Find all NEWS and SCIENTIFIC PUBLICATIONS here
Please find all project news here: https://www.etekina.eu/news/ and all Scientific Publications here: https://www.etekina.eu/scientific-publications/
Find all news here
Please have a look here https://www.laser4surf.eu/news/ to find all news about the project. Thanks!
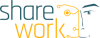
KEY FACTOR MOVEMENT PRIMITIVES: HOW CAN WE MAKE A ROBOT LEARN FROM HUMANS?
HOW DOES A ROBOT LEARN HOW TO PERFORM A TASK NOWADAYS?
Since Henry Ford’s assembly lines, automation systems have been developed and integrated in the industry all over the world. Clear examples of this are Amazon’s automated warehouses or Coca-Cola’s dark sheds.
While these examples are stunning, it is also true that nowadays, these robots need their own warehouses where no interaction with humans happens. Also, high qualified robotics engineers have to program them to perform the required repetitive tasks.
In the future, we imagine a world where anybody, without any prior knowledge in robotics, could buy a robot, set it in their workshop and start teaching the robot to perform some task interacting with the human workers. But, what should the robot learn? Welcome to the Movement Primitives.
WHAT ARE THE MOVEMENT PRIMITIVES?
Movement Primitives are the set models that represent the different type of actions the robot could do.These models will generate trajectories the robot should follow in order to perform a certain task.
Let’s assume we want a robot to learn to pick a certain object. Instead of programming the task, we can make the robot learn from human demonstrations. A human could move manually the robot arm to the object we want to pick several times while changing the object position and the robot will learn a model that represents that action. Afterwards, if the object is set in a completely new position, the robot will be able to generate a trajectory to pick this object.
MOVEMENT PRIMITIVES IN SHAREWORK
SHAREWORK project benefits from the use of Movement Primitives for task recognition and also prediction of human movement. Movement Primitives can represent the different type of motions the human does and so, they could be integrated as an additional feature for a task classification module. On the other side, Movement Primitives can provide a probabilistic prediction model about where the human is going to be, in order to improve the robot motion planners.
During the SHAREWORK project, Context-Aware Movement Primitive Segmentation algorithms are going to be applied. The algorithm will be able to segment the recorded human motion online and learn the simplest blocks of which the human motion is built in order to solve a complex task.
SHAREWORK project will use Movement Primitives for learning from human actions by understanding the worker’s behaviour and anticipating tasks
These learned motion primitives are contextualised with the objects in the environment in order to adapt to the different positions the same object can be placed. Afterwards, these Movement Primitives will be used as the building blocks of the task classification algorithms.
These same Context-Aware Movement Primitives will provide a probabilistic prediction of the position of the human in the future. Mixed with robot motion planner, the robot will plan safer trajectories, avoiding the collision with the humans.
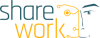
ROBOTICS INTO HANDWORK MANUFACTURING: THE FIGURE OF THE TECHNOLOGY COACH FOR LEADING AN EFFECTIVE AND SMOOTH IMPLEMENTATION
THE NEW CHALLENGE OF ROBOTICS: TAKE OVER THE HANDWORK MANUFACTURING
The Robotic Industry is growing bigger day by day, launching on the market several advanced solutions which promise to revolutionise the way factories produce goods and assembly parts in a near future. As a result, also the expectations of Industry are constantly increasing and they look at robots as the definitive solution to save time (and, of course, money) and boost profits of their manufacturing companies.
The handwork manufacture is the new battlefield that robotics has begun to conquest in recent years, but despite this there is still a lot of room for improvement and expansion. In fact, while nowadays almost all the operators performing repetitive and simple tasks have been replaced with highly automated assembly lines, the same has not yet happened for handcraft. This is mainly due by the fact that manual labour requires such high skills and a human sensitivity that, at the moment, a robot cannot replace the operator in almost all the cases.
The automation of assembly lines based mainly on handwork are quite a challenge for the robotic industry due to the need of high skills and sensitivity
The solution that robotic producers have found to overcome this limit is the launch on the market of collaborative robots (also called cobots). Cobots aim to support handcrafts in the most repetitive, heaviest and uncomfortable tasks rather than completely replace them, allowing to preserve the high quality generated by manual labour and speeding up the productivity at the same time.
Unfortunately, the implementation of a robotic system into the production process is everything except easy and instantaneous and the benefits the robot could bring are not so obvious. In fact, the selection of proper components and a smooth integration are crucial to generate the positive impact on productivity, quality and operators’ working conditions which factory owners wish. And this is even more true for the implementation of collaborative robots into handwork manufacturing, where the system should reach high performance without neglecting the operator safety and the human acceptance.
Collaborative robots offer handcraft industries a support in repetitive and uncomfortable tasks for operators
Indeed, there is the need of an intermediary figure which could drive the end-user through the jungle of robotic products and serve as an interface between the salesman approach of suppliers and the concreteness of craftsmen undertaking in the workshop. This figure within Sharework project is commonly named as “Technology Coach”, and STAM is in charge of filling that role for one of the four use-cases, namely the assembly of rotary table in Goizper factory.
THE TECHNOLOGY COACH: NOT ONLY A MATTER OF DESIGN
If the role of the Technology Coach is essential in the implementation of a robotic system into production lines, it could be even crucial when we talk about the introduction of cobots supporting handcrafts because of the aforementioned reasons. But exactly, who the Technology Coach is? And what it is supposed to do?
Generally speaking, it is a work team with well-mixed competences which belongs to a high-tech company or a R&D center. Unlike suppliers or system integrators, the Technology Coach not only proposes the design of a tailored robotic cell, but they follow a holistic approach which involves the end-user to reinvent and redesign the workflow and the workshop layout of tomorrow in a better way.
The Technology Coach should listen and understand the needs and the objectives of the end-user. Satisfying these wishes and achieving these goals will be its main mission. Once an agreement is found, Technology Coach should select suitable commercial solution, get in touch with suppliers, design the robotic system, reinvent the workflow and reshape the layout if needed, install and test the solution.They should take care of the whole process of implementation of the robot into the shop floor, from the definition of requirements to the commissioning and final test. This is an iterative and continuous process, some steps should be done several times until finding an equilibrium among the end-user expectations, the current robotic supply, the budget, the operator acceptance and well-being, the timing and so on.
Technology Coaches help industries in the implementation of new robotic systems, leading the whole innovation process matching he end-user’s demand in the most effective way
Most of the work of a Technology Coach can be done in its headquarters, using modern communication network to periodically update the end-user about the work progress. However, it is highly recommended to have a face-to-face with the end-user at the begin of the project, as well as to visit the shop floor and talk with operators working there to have a clear picture of the process.
The value added to the figure of the Technology Coach is to put at the stake all its set of cross-cutting competences and resources to satisfy the wishes of the end-user. Technical Coaching does not simply mean designing a robotic cell, but leading the whole innovation process of the manufacture, matching the robotic supply to the end-user’s demand in the most effective and smooth way.
THE SHAREWORK EXAMPLE: A COBOT FOR SUPPORTING THE MANUAL ASSEMBLY OF ROTARY TABLE
As mentioned before, STAM embodies the role of Technology Coach in Sharework project to support Goizper and coordinate partners contributions in the implementation of a collaborative robot system in their servo rotary table assembly area. As the assembly of these components requires a remarkable human sensitivity and manual skill, the main aim of Goizper is to delegate to the Sharework system the most heavy and repetitive tasks of the assembly, while preserving worker focus on the most skilled operations.
As first step, we worked together to select the most suitable tasks to be delegated to the cobot and to define in details each scenario. In order to have a complete and clear picture of the workshop and the process, we carried out a technical visit to the factory together with the consortium. We had the chance to directly experience the working conditions (e.g. spaces, loads, noise), as well as to talk in first person with the workers to collect their feedback.
Once the use-case was pretty defined, STAM began to serve as an interface among the end-user and the external world. Our role was double: on one hand we translated the requests of Goizper into requirements and clear specification to effectively communicate with commercial suppliers and with the multiple software developers involved in Sharework, each one focused on different specific tasks. And, vice versa, we collected feedbacks, requests and suggestions from all the different entities involved in the Sharework project to provide a unified vision to Goizper and to propose them a feasible human-robot collaborative solution that could meet their expectations.
For these purposes, 3D models and views (see the following pictures), as well as all the other visual medias, are very useful to finally put on paper the developed concept and allow other partners to understand it in an easy and clear manner.
It has been a long and iterative decisional process, but, in the end, we did it! We reached a final solution reinventing the rotary table assembly workflow to enhance the productivity, exalt the qualities of workers and safeguard their well-being.
However, our job is just starting out: we have to work hard in the next months to make this design on paper a concrete reality. Stay tuned!
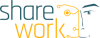
TRAVELLING TO GOIZPER 4.0 WITH COLLABORATIVE ROBOTICS ON BOARD
During the last years, Goizper’s mind has changed little by little, complementing new technology developments with the power transmission components portfolio. The obtained good results have certified that new technologies integration is the correct way to follow.
A STEP FORWARD BECOMING GOIZPER 4.0
Goizper S. Coop. has already integrated several Industry 4.0 solutions related to its market products, such as smart-G, an IoT monitoring system integrated on mechanical components in order to predict failures. However, now Goizper has started a new era introducing Industry 4.0 solutions on its own shop floor in Antzuola, Basque Country (Spain).
On the one side, new machinery, such as milling and turning machines, are running in Goizper’s shop floor, with integrated IoT solutions and direct connection with the supplier (machine experts) through internet. On the other side, Goizper has decided to invest in new technologies on the manual assembly area, where operators’ ergonomic issues concern the company.
Conventional robots have never fit in the assembly area due to the flexibility degree that Goizper’s products assembly require and the high variety and low quantities of each reference. However, Goizper decided to go further and participate in Sharework project as we believe that collaborative robots will be able to provide the flexibility that Goizper’s assembly area needs. Within the project, Goizper Industrial will validate a new design of their workplace to introduce collaborative robots in their servo rotary table assembly area.
Several benefits are expected from Sharework project, including an improvement of ergonomics in the workplace, avoid work-related injuries, improve the final quality of the product and a significant reduction of the assembly process’ cycle time.
OPERATORS’ ERGONOMICS CONDITIONS TO IMPROVE
A new way of introducing robotics into the workplace has risen with the development of collaborative robotics (Cobots), which allow the operator to share the assembly area with robots without the need to be separated by fences. Managers in Goizper think that Cobots introduction in the assembly line by means of Sharework project, will improve operators´ ergonomics conditions.
Power transmission components’ assembly, such as turning tables, request many manual adjustments applied by human force. Hence, some tasks could lead to back injuries or muscular pain in operators.
OPERATORS AND COBOTS, A SUCCESSFUL TEAM TO RISE PRODUCT QUALITY
For sure, with the introduction of cobots for operators’ assistance, the quality of the assembled product will be higher. Obviously, automated processes provide a higher percentage of good parts compared to manual processes. In Sharework industrial scenario, bolts will be locked with the same torque in a repetitive and more precise tool than nowadays.
Goizper is eager to see how much the quality of their products is improved after cobots incorporation, during Sharework project.
SPEEDING UP THE ASSEMBLY PROCESS
Productivity is not the main goal of this technology integration; nevertheless, assembly cycle time is expected to be reduced due to the fast execution of UR10 Cobots. Within Sharework scenario, which will be applied to our servo rotary table assembly area, time reduction must provide a better lead time of the product and economic benefits.
THE SAFETY OF OUR EMPLOYEES AT THE CENTER OF ALL THE OPERATION
As none of these new technology’s integration could run before ensuring human safety and make sure that all safety requirements in the shop floor are met, Goizper’s Human Resources Department – the bridge between the new technology and the human – is also closely participating in Sharework project.
Goizper, as one of Sharework’s project industrial scenarios, aims to use the collaboration robotics technology for assisting and helping operators in their daily tasks, such as handling heavy parts to the operator and passing them the correct part to be assembled or the tool to be used at the correct time. Under no circumstances the operator will be replaced by the collaborative robot but just another tool available to help for the operator, in addition to other technologies or devices already deployed in the assembly workplace.
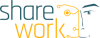
CEMBRE AND THE SHAREWORK PROJECT: A STORY ON COLLABORATIVE ROBOTS’ DEPLOYMENT IN FLEXIBLE MANUFACTURING ASSEMBLY AREAS
The manufacturing industry is observing great changes in these years. Its radical evolution is due to the growing demand of the market, accompanied with an increase of variety. Both these characteristics force us to gain more flexibility, accuracy and efficiency in our production departments, together with a continuous cost reduction.
The industrial manufacturing applications have seen the introduction of a new category of robots – collaborative robots (or “cobots”) – designed to physically interact with humans in a shared environment, without the typical barriers or protective cages used in traditional robotic systems.
Our vision in Cembre S.p.A. is to take advantage from cobots and from the smart manufacturing as a whole in order to increase the service rate and improve the worker’s ergonomics. We think that human-robot collaboration (HRC) is prime for increasing both these factors and that Sharework EU project is fundamental for developing more knowledge about HRC, helping filling the gap between the robotic and the human worlds.
Cembre could have gone to full shop floor automation but we would have lost human flexibility. Collaborative robots provide a half way solution between the human and robotics world
THE INTRODUCTION OF COLLABORATIVE ROBOTICS IN ADVANCED MACHINE TENDING
Cembre S.p.A., based in Brescia (Italy), is always eager to employ new methods or technologies that can support the development and the improvement of its entire production system. For this reason, the company constantly collaborates with universities, start-ups, research centres and others associations.
The Sharework project perfectly fits in this approach, since it will be pioneering in the employment of HRC using collaborative robots within manufacturing systems and, in general, in industrial operations.
The objectives we want to achieve are many.
- Gain flexibility in managing the machining of a large variety of parts without the need to develop expensive equipment and plan a long training for every new product that enters the shop floor.
- Employ our operators in more value-added tasks, such as inspections and process optimisation, and move non-value-added activities and repetitive task, such as motion or transportation, to the cobots.
- Increase operators’ ergonomics, which itself is one of our primary targets together with operator’s welfare and satisfaction. These latter should increase because the skills required to an operator will be brought to a higher level thus improving the interest for the job inside machining shop floor.
- In the long term, once the complete system will be deployed on the whole shop floor, we also expect a decrease in lead-time and quality losses.
SHAREWORK PROJECT DEPLOYMENT AT CEMBRE’S PLANT
We are currently implementing the Sharework project in the machining shop floor located in Brescia’s plant: production engineers, human resources and operators are all engaged. Most of them are new to this kind of projects and these technologies, aspects that makes Sharework especially challenging for the company. Regarding this, the contributions of the CNR, the Italian research centre, and of MCM, our technologic partner, are very important to us.
The role of people is fundamental to create deep connections between working conditions and technologies. In fact, one of the main challenges for the future is to understand how this new paradigm for the manufacturing systems could generate benefits to the entire production chain. Who if not humans could imagine this?
UPTIME Newsletter - June 2020
Welcome to the 6th edition of the UPTIME Newsletter!
The UPTIME project has entered the evaluation phase. The prototype of the UPTIME Platform has been integrated into the three industrial business cases in its final configuration. In this edition, MAILLIS shares with us their first-hand experience and some lessons learned from the recent implementation of the UPTIME Platform in the MAILLIS Business Case, which deals with predictive maintenance in a cold rolling mill for the production of steel strapping.
In the previous newsletters, we introduced five of the UPTIME Platform’s main components. In this issue, we’ll present the last component prototype, UPTIME_VISUALIZE, which provides individual, customizable and configurable visualisation of data in a customer-oriented way. Its implementation in the MAILLIS Business Case is used as an example of how it works.
We have also been organising a series of webinars showcasing the main features of the UPTIME Platform including live demonstrations of their implementation in our industrial use cases. The first webinar on the implementation in the White Goods case was held on 19 March 2020. In case you missed it, you can find the webinar recording here.
The second webinar, “UPTIME Predictive Maintenance: Lessons Learned and Best Practices in the Steel Industry“, will take place on Thursday, 09 July 2020, 11:00 – 12:30 CEST. We hope you can join our webinar and look forward to interacting with you and getting your valuable feedback. To register and get more detailed information about the webinar, please click here. We hope you enjoy our newsletter!
A full newsletter is available: https://www.uptime-h2020.eu/index.php/2020/06/26/uptime-6th-newsletter-edition-06-2020/
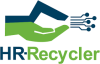
CERTH explain their work in AI-enabled Cell-level perception methods
The objective of this task is to provide the envisaged robot with the ability to perceive the industrial environment so as to effectively collaborate with the humans and assist them with the Waste Electrical and Electronic (WEEE) device recycling process. Towards this direction, CERTH recorded multiple recycling procedures of four WEEE devices, namely PC Towers, Microwave Ovens, Flat Panel Displays and Emergency Lamps, focusing on the human-robot collaboration aspect during the WEEE device disassembly, thus creating a WEEE device component detection dataset by manually annotating a number of the recorded frames.
Given this dataset, CERTH deployed state of the art Computer Vision methods utilizing Deep Learning techniques in order to train a Convolutional Neural Network (CNN) capable of detecting the four WEEE devices as well as their respective components during the various stages of the disassembly process. Additionally, CERTH enhanced these methods by proposing an anchoring mechanism targeting specifically the detection of small objects.
https://www.hr-recycler.eu/certh-explains-their-work-in-ai-enabled-cell-level-perception-methods/
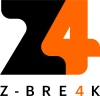
Z-BRE4K Presentation video is online!
Have a look at Z-BRE4K presentation video and discover more on our Predictive Maintenance solutions!!
Link to: https://youtu.be/k1aZKtPpADQ
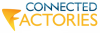
EFFRA consultation Made In Europe Partnership
Currently, EFFRA carries out a consultation consisting of two main tracks.
- One track aims at collecting the opinion of individual experts who respond on behalf of their organisation (or on behalf of a part of their organisation)
You can find more information about this consultation here.
- The other track collects information from the perspective of finished or ongoing European Projects, in particular addressing Factories of the Future PPP projects, but not excluding other relevant projects.
You can find more information about this consultation here.
The deadline for the Made In Europe’s consultations is extended until 30 of June.
Stay up to date: https://www.effra.eu/made-in-europe-state-play