The subject of the collaborative process is the assembly of a part of the car starter for a car manufacturer. This part of the process comprises of inserting copper sliding rings into metal pallets, which are then transferred to the molding machine. Currently, the process of inserting sliding rings into the pallet is performed manually and is considered hard to automate. The process is demanding due to the high flexibility and elasticity of the sliding rings.
Previous attempts of automation failed for two reasons:
- it was not possible to grasp the sliding rings, because they are often stuck together on the transport plate;
- it was not possible to assure the required success rate of the insertion due to the flexibility and elasticity of the rings.
The vision of the project is to develop a robotic system that will assist the worker or even replace the worker when he will not be present. Therefore, with the worker and the robot both capable of executing the same operations, the work sharing will be assigned dynamically.
The task of the worker will be to a) grasp the rings from the transport pallet and put them on the table, and b) to supervise the assembly and correct it if necessary. The worker will often leave the cell, since he will have to supervise also other production cells.
Insertion of a slide rings can be divided into three phases: grasping the part from the table, where the part position is not defined in advance, rough insertion of the part and fine adjustment of the part.
The initial learning will be accomplished by observing humans using technology developed in WP4. From this data, the system will generate approximate trajectories and probabilities associated with the confidence of the captured trajectories. In the next learning stage, the operator will manually guide the robot along this trajectory and perform fine tuning (WP4). After the learning, the robot will start with exploitation phase and autonomous refinement of the assembly trajectory (WP4).
The objective for learning will be to minimize the contact forces and torques and to successfully accomplish the assembly task. Success of the assembly operation will be determined from a) observing whether human operator had to correct the assembly; and b) from vision sensor, where the system will learn from the human feedback. Grasping deviations will be detected using precise RGBD sensor. In order to generalize to the different grasping situations, we will apply deep Q learning algorithms, which will map RGBD image to the assembly policy.
The benefit of this cooperative automation will be in a shorter cycle time. Moreover, the system will become more and more autonomous and hopefully would need less and less assistance from humans. Note that in a modern production, humans normally assist more than one work cells and it is less likely that humans would tightly cooperate with other humans all the time. This use case will be the pilot case for many similar work-cells in “Kolektor” factory.
Although “Kolektor” is not an SME, there are plenty of work processes that do not justify fixed automation, as this would elevate the production cost in low-batches production and increase the setup time. By applying reconfigurable hardware elements, the same work cell will be used in many operations that are currently performed manually. This concept has a great dissemination potential to many tasks in SME and craft production.
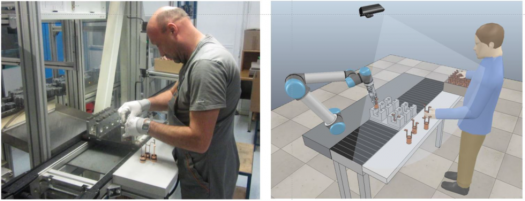
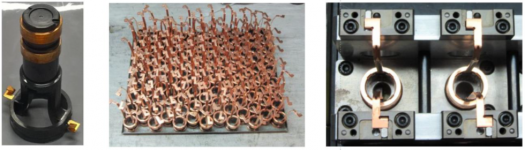
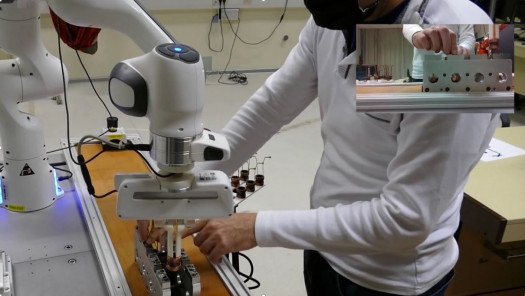