In current general assembly production lines, different use cases require phases of visual inspections and preassembly. While for most of the cases the handled parts are small or relatively small, that means that the operation is easy to be performed manually, in some cases the operation requires the handling of cumbersome or heavy parts to be performed with the aid of manual supports (also known as partners: zero weight support manipulators). In these case the operation becomes difficult and requires awkward positions to be performed or eventually the presence of additional fixed supports like table, fixtures and so on.
The CRF use case in the CoLLaboratE project is a use case in which both assembly operations and visual inspections are important on a part which is heavy, cumbersome and fragile. The reference part is the windshield which, according to the reference plant, has additional manual operations to be performed by the operator.
The use-case doesn’t aim at the effective modification of an existing line, but it is focused on the realization of a new workcell in which:
- a front windshield is picked up and manipulated;
- a visual check of the state of the product is performed to check cleanness & existence of cracks;
- a series of manual assembly phases is performed on top of the windshield in a collaborative way;
- the robot completes the assembly of the windshield on the chassis (gluing if necessary, positioning).
As for the ergonomics considerations in the workcell, the use of the robot allows the implementation of a workcell which is constantly in Golden zone for all the work phases.
To show this approach an initial concept layout of the gripper have been made with a detail of the manipulation zones onboard of the gripper. On the manipulation zones (which could be retractable to ensure both the pick-up phases from the container) it is planned to install a sensitive skin which, properly interpreted, will furnish information on forces, activities and willingness of the actions performed by the operators.
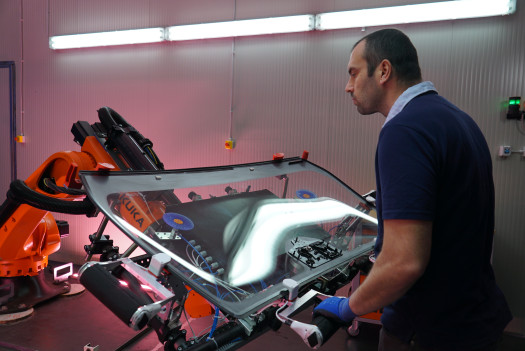
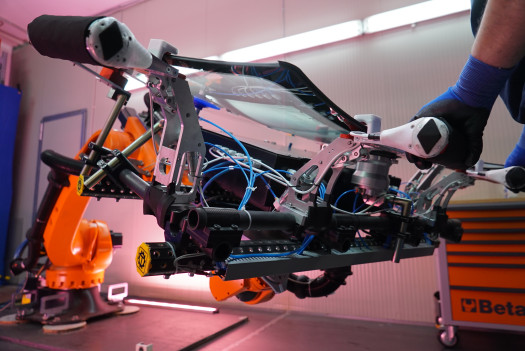