Scale-up Proof-of-concepts are the finest the Reboot has to offer. They are the proof-of-concepts that are so successful that they are taken to another factory already during the project.
Tester Predictive Maintenance proof-of-concept arose from the need of detecting when a tester is breaking down and not the products it is testing. Research was done towards how the testing data from the tester could be analysed in a way that it would indicate the wear and tear of the testing equipment. The first implementation was done at Nokia factory for electronics needs. The proof-of concept were a success and the algorithms could be applied to find the testing equipment failure. As data is gathered more the more efficient the analysis become.
Often the simplest solution to a problem is also the most effective. In order to discover such solution one has to take a step back and look for new points of view. To think outside of the box, as the saying goes. This is what happened at Nokia in Oulu, in Reboot IoT Factory’s TesterWatch project. As the outcome a novel way to test the functioning of base station products was invented.
Before shipping to customers, the proper functioning of base station products is ensured with test devices. Parallel identical test devices are used for scaling up the operations. If one tester gives systematically different readings than its peers, the problem is likely in that particular tester, not in the product which is being tested. For example the connectors used to attach test devices with products start to wear down over time. This causes contact failures and the test results start to fluctuate. Anomalies result in sending a real time alarm to the maintenance team. This way quality engineers can immediately engage in repair activities. Before TesterWatch they run reports in mornings and based on those performed the needed actions.
The algorithm itself and the solution based on it are straightforward. They were born in a brainstorming session among the project team followed by statistical analysis. The analysis and number crunching was completely agnostic to base station technology. Exactly this is the out of the box approach. The solution most likely would not have been invented if the project team had consisted only of the base station factory’s own workforce.
The approach can be extended to other industry domains. Reboot IoT consortium has introduced it in GE’s factory in Vallila, Helsinki where predictivity ability has been researched and implemented. Naturally also Nokia is going to implement it in its other factories. In Oulu it is already used in production 24/7.
TesterWatch is a prime example of digitalization project which delivers new process innovations rather than tangible gadgets. Testing base station products is now more reliable than it was before. Time and money get saved.
Even though the current version of TesterWatch is quite simple, it can be developed towards machine learning and AI. The aim is to enable predictive maintenance. Today’s maintenance team is called when something has already happened. In the future they can be paged before things go wrong. The system can for example keep log of test devices’ functioning and propose changing some parts to a particular device once it reaches certain age.
TesterWatch can also be attached with a broader digital system of a factory.
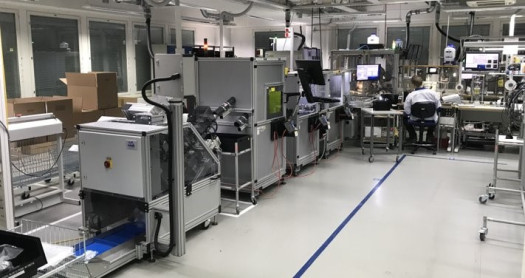
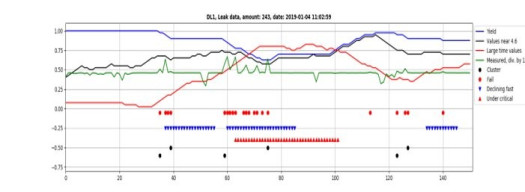