Experiment description
Zannini SPA produces high precision mechanical components for hydraulic and pneumatic systems for cars and household appliances. The quality control of this components is at this moment, ran only on a stastistical basis and there is no real-time feedback for adjustment of the process parameters. This leads to undesirable process settings, a high waste rate and a low-capacity index. The current monitoring process does not take into account all available quality data for improving the components quality.
Enabling real-time montioring and analysis will help the production process in order to identify anomalies and divergences at the moment of yielding the components. The HPC platform will execute and process the huge amount of data which will be produced from Zannini manufacturers, in order to run the simulations needed.
Technical Impacts
In this project, Nissatech wants to adapt its new solution: the Data-driven Twin (D2Twin) to Zannini processes. This new solution models the behaviour of a system through a reverse engineering from the company’s old data to new advanced data. This results in an automatized process without any human intervention.
This solution extends the common concept of digital twin by integrating the perspective regarding how the object has been used in the past. It can be used in any domain where data is available.
Web resources: | http://bit.ly/2Eq5HCA |
Country: | IT |
Address: | Via Che Guevara 63/A, Castelfidardo 60022 |
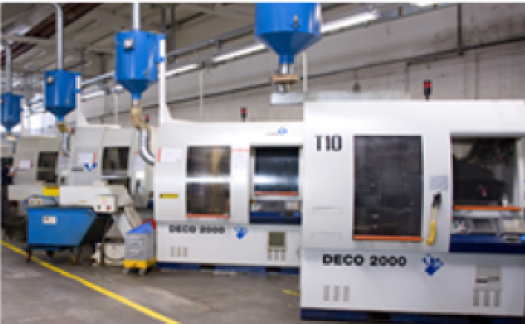